Professional solutions on concrete addtives, Concrete Foaming Agent, Superplasticizer, CLC Blocks Additives, and foaming machine
Polyacrylic acid (PAA) is a high molecular weight polymer that has become an indispensable component in many industrial applications, from water treatment to personal care products. Most notably, it is a key ingredient in the formulation of high-efficiency water-reducing agents for concrete. This multi-purpose polymer derived from acrylic acid has unique properties such as excellent water solubility, biodegradability, and chelating ability, making it the preferred choice for many chemical processes. However, its synthesis, especially when using large amounts of acrylic acid, presents significant challenges, particularly in terms of temperature control during the polymerization process. This article delves into the complex role of PAA in modern chemistry, with a particular focus on addressing temperature control issues related to the use of high acrylic acid.
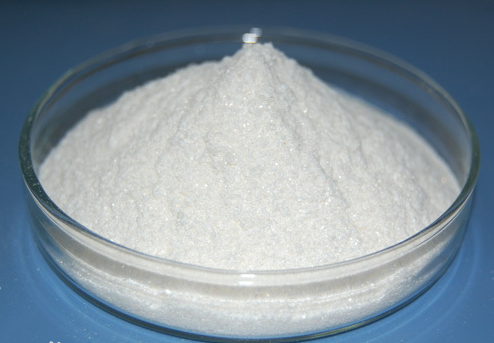
Polyacrylic acid
The universality of polyacrylic acid
The multifunctionality of polyacrylic acid stems from its carboxylic acid functional group, which can be modified to produce various derivatives. These derivatives have applications in multiple fields, including pharmaceuticals, where they are used as drug delivery systems, and the construction industry, where PAA-based high-efficiency water reducers can improve the workability of concrete. The ability of polymers to form strong hydrogen bonds and their ability to act as chelating agents make them ideal candidates for these and other applications.
In the context of superplasticizers, PAA and its derivatives, such as polycarboxylate ethers, are crucial for improving the flowability of concrete mixtures. They achieve this by dispersing cement particles more effectively, thereby reducing the required amount of mixing water. This not only improves the workability of concrete but also enhances its strength and durability. The performance of these superplasticizers largely depends on precise control of the polymerization process, including the use of specific monomers and reaction conditions.
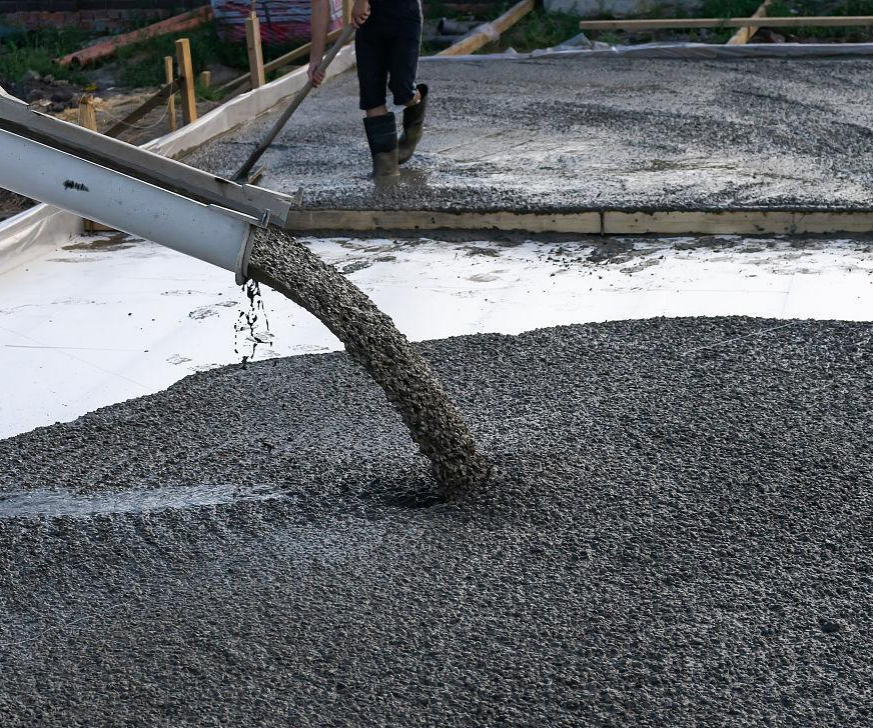
Polycarboxylate ether improves the flowability of concrete
The challenge of temperature control in the use of high acrylic acid
One of the main challenges in PAA synthesis, especially when using high concentrations of acrylic acid, is to maintain the reaction temperature within a narrow range. The polymerization of acrylic acid is exothermic, which means it releases a large amount of heat. If properly controlled, this heat can lead to uncontrolled reactions, resulting in consistent molecular weight and better quality of the product. Traditional temperature control methods, such as cooling jackets or external heat exchangers, may be energy-intensive and may only sometimes provide the necessary accuracy.
The demand for precise temperature control becomes even more critical in the production of PAA for special applications such as high-efficiency water reducers, as the structure and properties of the polymer must be finely tuned. In these cases, even small deviations in temperature can significantly affect the performance of the final product. For example, overheating can lead to premature crosslinking, causing gelation or the formation of insoluble polymers, which is not ideal in many applications.
Parameter | Value |
Chemical Name | Poly(acrylic acid) |
CAS Number | 9003-01-4 |
Molecular Formula | (C3H4O2)n |
Average Molecular Weight | Varies, typically from 1,000 to >1,000,000 Da (depending on the grade) |
Appearance | White to slightly yellowish powder or granules; can also be in solution form |
pH of 1% Solution | 2.0 – 3.0 (at 25°C) |
Solubility in Water | Soluble in water, insoluble in most organic solvents |
Viscosity @ 25°C (for solutions) | Variable, depends on concentration and molecular weight |
Density (solid form) | ~1.3 g/cm³ |
Acid Value | ≥ 560 mg KOH/g (for dry polymer) |
Residue on Ignition | ≤ 0.1% |
Moisture Content | ≤ 10% (for solid forms, varies with grade) |
Storage Conditions | Store in a cool, dry place. Keep container tightly closed. Avoid exposure to moisture and heat. |
Shelf Life | 2 years when stored under recommended conditions. |
Product parameter table of polyacrylic acid
Exploring Solutions: Alternative Solutions to Traditional Temperature Control
Given the challenges associated with traditional temperature control methods, researchers and industry experts have been exploring alternative methods for managing the exothermic properties of acrylic acid polymerization. A promising solution involves the use of automated aggregation technology, which inherently reduces the risk of overheating. These technologies include:
Selection and dosage of initiators: By carefully selecting initiators that decompose at lower temperatures and administering them in a controlled manner, the polymerization rate can be slowed down, resulting in better heat dissipation. Initiators with clear decomposition characteristics, such as azo compounds and peroxides, can be used to achieve this effect.
Control of monomer feed rate: Another method is to control the feed rate of acrylic acid monomer. By gradually adding monomers to the reaction mixture, the heating rate can be controlled to prevent sudden temperature spikes. This method requires complex dosing equipment and real-time monitoring to ensure consistent and accurate addition.
Use of radiator monomers: Adding radiator monomers such as methyl acrylic acid or other monomers with higher activation energy can help absorb excess heat generated during the polymerization process. These monomers act as buffering agents, stabilizing the reaction temperature and preventing thermal runaway.
Microencapsulation technology: Microencapsulation of initiators or monomers can delay the start of polymerization reactions, thereby better-controlling heat release. This technology involves encapsulating reactive components in a protective shell, which gradually dissolves or degrades during the reaction process, releasing the contents in a controlled manner.
In situ cooling methods: Some innovative in-situ cooling methods, such as using phase change materials (PCM), can be used to absorb and store heat during exothermic reactions. PCM undergoes a phase transition at a specific temperature (such as from solid to liquid), which can effectively manage the generated heat and maintain a stable reaction temperature.
Continuous flow reactor: Continuous flow reactors provide a more controllable environment for the polymerization of acrylic acid. By continuously feeding reactants and removing products, these reactors can maintain a stable state, minimizing the risk of temperature fluctuations. In addition, the smaller the volume of the reaction mixture in the continuous flow reactor, the higher the heat transfer efficiency, further strengthening temperature control.
Polyacrylic acid has a wide range of applications and remains an important material in modern chemistry. Solving the temperature control challenge during high acrylic acid concentration polymerization is crucial for ensuring the quality and performance of PAA-based products. By adopting innovative solutions such as controllable monomer addition, use of heat sink monomers, and microencapsulation, the industry can overcome these challenges and produce high-quality PAA with higher efficiency and sustainability. With continued research and development, PAA has broad prospects in advanced polymer chemistry, with the potential for more innovative and effective applications.
Supplier
Cabr-Concrete is a supplier under TRUNNANO of Concrete Admixture with over 12 years of experience in nano-building energy conservation and nanotechnology development. It accepts payment via Credit Card, T/T, West Union and Paypal. TRUNNANO will ship the goods to customers overseas through FedEx, DHL, by air, or by sea. If you are looking for Polyacrylic acid, please feel free to contact us and send an inquiry.sales@cabr-concrete.com