Professional solutions on concrete addtives, Concrete Foaming Agent, Superplasticizer, CLC Blocks Additives, and foaming machine
PRODUCT PARAMETERS
Description
Introduction of high-performance polypropylene fibres (PP fibres)
Introduction: Polypropylene fiber (PP fiber) is made of polypropylene and a variety of organic and inorganic materials through a special composite box, made. Specific gravity 0.90-0.92g/c ㎡, bundled monofilament, melting point 160-176 ° C, diameter 18-48μm, non-toxic, odorless. Polypropylene fiber’s standard moisture return rate is almost zero, hydrophobic moisture conductivity has the best performance, and it has better resistance to acid and alkali and heat aging properties.
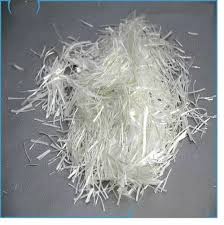
Performance Characteristics of Polypropylene Fiber Silk:
Polypropylene, as the primary raw material for the manufacture of high-strength bundled fibers, added to the concrete or mortar can effectively control the concrete (mortar) solid plastic shrinkage, dry shrinkage, temperature changes, and other factors caused by micro-cracks to prevent and stop the formation and development of cracks, significantly improve the crack-blocking and impermeable properties of the concrete, impact resistance and seismic capacity. Polypropylene fibers are not hydrophilic, do not disperse nicely in concrete, and do not combine well with concrete, which limits the improvement of the performance of polypropylene fiber-reinforced concrete. Through the hydrophilic modification of the surface of polypropylene fibers or modulation of the fiber morphology, the dispersion and bonding of polypropylene fibers in concrete can be significantly improved, and the anti-freezing and anti-cracking properties of concrete can be enhanced.
Performance Characteristics of Polypropylene Fiber Silk:
Polypropylene, as the primary raw material for the manufacture of high-strength bundled fibers, added to the concrete or mortar can effectively control the concrete (mortar) solid plastic shrinkage, dry shrinkage, temperature changes, and other factors caused by micro-cracks to prevent and stop the formation and development of cracks, significantly improve the crack-blocking and impermeable properties of the concrete, impact resistance and seismic capacity. Polypropylene fibers are not hydrophilic, do not disperse nicely in concrete, and do not combine well with concrete, which limits the improvement of the performance of polypropylene fiber-reinforced concrete. Through the hydrophilic modification of the surface of polypropylene fibers or modulation of the fiber morphology, the dispersion and bonding of polypropylene fibers in concrete can be significantly improved, and the anti-freezing and anti-cracking properties of concrete can be enhanced.
Technical Characteristics:
(1)Easy to Disperse in Mortar Or Concrete, Not Easy to Settle, Effectively Ensure Its Anti-Crack Performance.
(2)Easy to Use, No Need to Change the Mortar Ratio, Fiber and Concrete Aggregate, Admixture, Admixture, and Cement Will Not Have Any Conflict, There Is No Special Requirement for Mixing Equipment. Put the Fiber into the Mortar Mixture and Stir Evenly
(3)More Conducive to Hanging Ash Because the Fiber Fineness Is Large and Evenly Distributed in the Mortar, More Conducive Hanging Ash Improves the Bonding Strength of the Plastering Surface and the Substrate.
(4)The fiber has stable chemical properties and strong acid and alkali resistance, and it can be applied to any field of engineering.
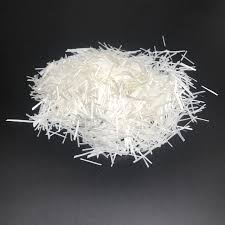
Construction Technology:
According to the Design Dosage and Concrete Mixing Method, Accurately Weigh the Fiber after Preparing the Sand and Gravel, Add the Fiber Together with the Aggregate to the Mixer, Appropriately Extend the Mixing Time for 30-60 Seconds, and Randomly Sample after the Mixing Is Completed. If the Fiber Has Been Evenly Dispersed, the Concrete Can Be Put into Use. If There Are Still Bundled Fibers, the Mixing Time Can Be Extended by 30 Seconds, and It Can Be Used. The Concrete with Fiber Is the Same as Ordinary Concrete Construction and Curing Process.
Suggested Admixture:
Ordinary Plastering Mortar Suggests That the Amount of Mortar Per Party Is 0.9-1.2kg, Generally 1kg/㎡; The Recommended additional amount of Thermal Insulation Mortar Per Ton Is 1-3kg; It Is Suggested That the Content of Concrete Per Party Is 0.6-1.8kg, Generally 0.9kg/㎡.
Scope of Application:
1. Used for Basement Pouring, Plastering of Interior and Exterior Walls, Water Power, Electricity, Tunnels, Swimming Pools, Etc. It can Improve Crack Resistance, Impermeability, and Frost Resistance.
2. It Can Be Used in Highway Bridges, Airports, and Other Projects to Improve Impact Resistance, Earthquake Resistance, and Wear Resistance.
3. Used for Spraying Mortar Concrete to Improve Compressive Strength, and Rebound Loss Rate Is Greatly Reduced. Used in Mortar, Concrete Precast Components improve the overall crack resistance of the component and provide adequate reinforcement protection for the corners of the precast.
4. The Aspect Ratio of Fibers for Concrete Is Generally above 400. The Repulsion Generated by the Surface Modification of the Staggered Fibrillated Fiber Bundles Can Be Easily Dispersed in the Matrix. Although the Chemical Bond Connection Is Limited, the Mechanical Bonding Is Good So That the Fibers Are Not Pulled Out When Stressed.
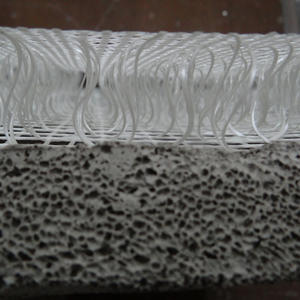
Main Characteristics of Polypropylene Fiber:
①Polypropylene Fiber Has High Strength, Good Elasticity, Wear Resistance, and Corrosion Resistance;
②Polypropylene Fiber Has Good Insulation and Warmth Retention;
③Polypropylene Fiber Is Very Light in Weight, High in Strength, Wear-Resistant and Elastic, Corrosion-Resistant. Fabric Fibers Are Different from Those Used in Concrete. If you have any Consultations for other purposes, you can ask for technical parameters.
Packaging Methods, Storage, and Transportation Precautions: 10kg, 180kg Bags, Compressible, Pallet. Store in a Cool, Dry, and Ventilated Warehouse.
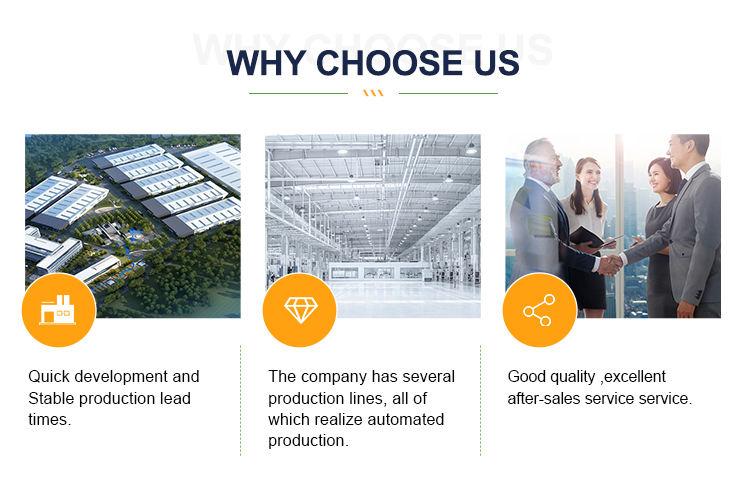
Company Profile
Cabr-Concrete is the global leader in Low-Density Cellular Concrete (LDCC), Celluar Light Concrete (CLC), and advanced engineered foam solutions. Known globally for its commitment to research, innovation, and applied expertise, we have been providing engineered foam solutions since the early 2012’s.
We can supply Calcium formate over the world. The company has a professional technical department and quality supervision department, a well-equipped laboratory, and equipped with advanced testing equipment and after-sales customer service center.Send us an email or click on the needed products to send an inquiry.
If you want to know more about Polypropylene fibres (PP fibres), please feel free and contact us: sales1@cabr-concrete.com
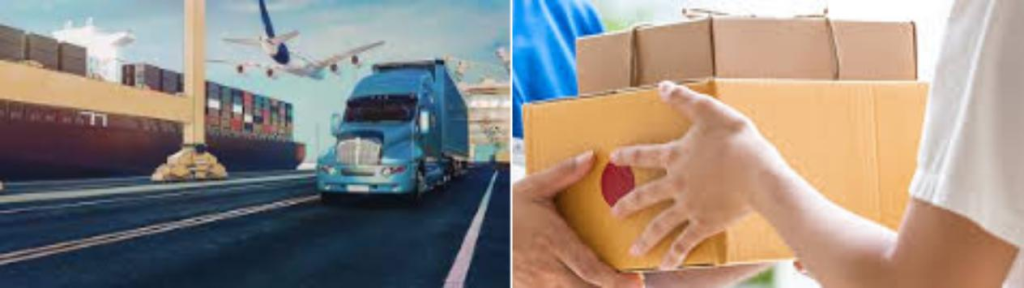
Payment
T/T, Western Union, Paypal, Credit Card etc.
Shipment
By air, by sea, by express, as customers request.
REQUEST A QUOTE
RELATED PRODUCTS
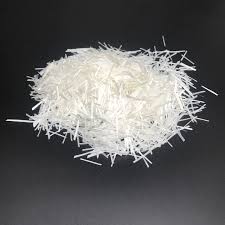
High Quality Fiberglass Chopped Strands Alkali Free Glass Fiber Chopped Strand For Concrete Use
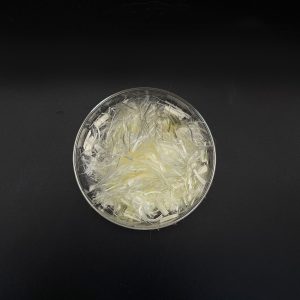
Pan Polyacrylonitrile Fiber for Construction and Raw Materials
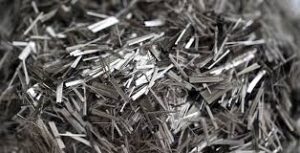
Wholesale Price Basalt Fiber High Strength Basalt Fiber Rebar Basalt Fiber Reinforced Composite Rebar For Concrete
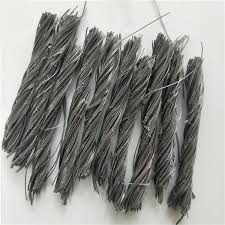
High Quality Polypropylene Bundled Fiber For Concrete Using
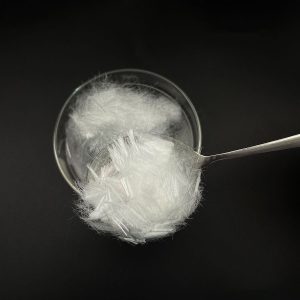
UHPC Special High Performance Polypropylene Synthetic Fiber
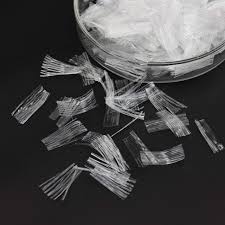