Professional solutions on concrete addtives, Concrete Foaming Agent, Superplasticizer, CLC Blocks Additives, and foaming machine
The global construction sector faces unprecedented demands as urbanization accelerates and climate resilience becomes non-negotiable. Distributors concentrating on innovative concrete solutions are currently at the center of this transformation, delivering products that redefine resilience, effectiveness, and sustainability. Amongst these technologies, superplasticizer admixture stands out as a game-changer, enabling ultra-high-strength concrete with unrivaled workability while lowering water material by about 40%. This breakthrough not only addresses labor shortages by streamlining pours but likewise lines up with worldwide net-zero objectives by lowering cement usage.
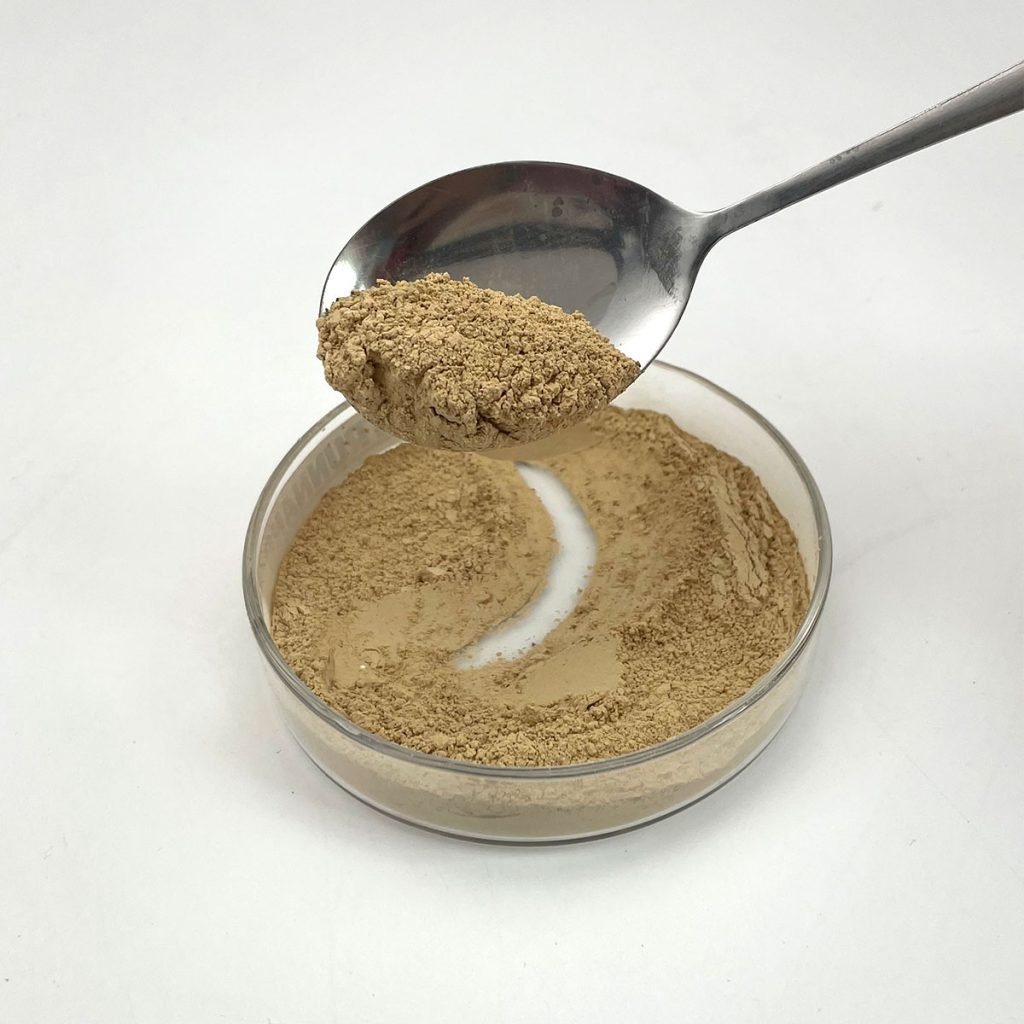
superplasticizer admixture
Superplasticizer in concrete isn’t simply a technological enhancement– it’s a necessity for modern infrastructure. From high-rises in Dubai to earthquake-resistant bridges in Japan, this additive ensures accurate flowability without jeopardizing architectural stability. Companies around the globe report quicker job timelines and lowered labor costs, making it important for high-stakes tasks. For instance, the ongoing expansion of Singapore’s metro system depends heavily on superplasticizers to accomplish thick reinforcement in constrained areas. Without such additives, delays because of concrete setting problems could cost millions daily.
Yet, durability extends beyond stamina. Go into concrete waterproofing additive, a quiet hero combating rust and prolonging the life expectancy of below-ground frameworks. In flood-prone areas like Southeast Asia, these additives prevent catastrophic water access, saving millions out of commission prices. A current instance in Vietnam’s Mekong Delta saw a 70% decrease in basement leakages after integrating waterproofing representatives throughout the mixing phase. Similarly, cement waterproofing additives are incorporated seamlessly throughout production, developing an impenetrable obstacle that outlasts standard layers. Unlike surface-applied membrane layers, which break down under UV exposure, these additives secure concrete from within, making them suitable for coastal frameworks.
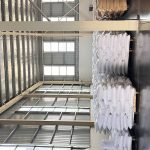
Cement waterproofing additives used in the construction industry
For crack control and impact resistance, concrete fiber additive is reshaping industrial flooring and pavements. Steel or polymer fibers dispersed within the mix absorb stress, reducing fissures by over 60%. A recent highway project in Germany credits this additive for its zero-maintenance record post-construction. The fibers act as a microscopic reinforcement network, distributing loads evenly and preventing localized failures. In cold climates, where freeze-thaw cycles wreak havoc, synthetic fibers have proven critical. Canadian contractors, for instance, now mandate fiber additives for all public roadways after a pilot project in Alberta showed a 45% drop in pothole formation.
Sustainability remains a driving force. Modern superplasticizers now incorporate bio-based polymers, cutting carbon footprints while maintaining performance. One Nordic supplier reported a 30% surge in demand after introducing a recyclable formula aligned with EU green standards. These eco-friendly variants use lignin—a byproduct of paper manufacturing—to replace synthetic chemicals. Meanwhile, researchers in India are experimenting with rice husk ash as a supplementary material for superplasticizer admixture, turning agricultural waste into high-value additives. Such innovations not only reduce landfill burdens but also lower production costs by up to 18%.
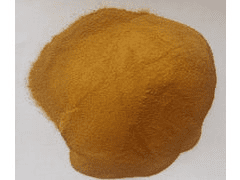
superplasticizer admixture
Combining markets is catching on. African nations, dealing with quick urban spread, concentrate on affordable choices like hybrid admixtures integrating waterproofing and plasticity. Kenya’s affordable realty effort, as an example, uses blended ingredients to decrease product expenditures by 25% while satisfying rigorous toughness requirements. Meanwhile, smart cities in China demand ingredients suitable with 3D-printed concrete, pressing R&D teams to introduce non-stop. A Shanghai-based startup just recently introduced a superplasticizer in concrete customized for robotic extrusion, making it possible for elaborate building designs formerly considered difficult.
Global partnership gas progress. A recent partnership between Brazilian engineers and Indonesian suppliers birthed a tropical climate-specific superplasticizer, resisting humidity-induced curing delays. This product now dominates Southeast Asian markets, where monsoons traditionally stalled construction for months. Similarly, Egyptian and South Korean firms co-developed a cement waterproofing additive infused with nanotechnology, which repels saltwater corrosion in desalination plants. Such alliances prove that localized challenges demand globally informed solutions.
Regulatory shifts also play a role. Stricter building codes in hurricane-prone zones now mandate fiber-reinforced concrete, propelling demand for concrete fiber additive. After Hurricane Maria devastated Puerto Rico’s infrastructure in 2017, updated regulations required all public buildings to incorporate steel fibers. Suppliers who preemptively certified their products gained a competitive edge, capturing 80% of the island’s reconstruction contracts. In earthquake-vulnerable Chile, laws now enforce the use of superplasticizer admixture in high-rises to ensure fluid concrete fills every reinforcement crevice.
Cost remains a hurdle, but lifecycle analyses sway decisions. A Malaysian port authority found that investing in premium cement waterproofing additive saved 50% in maintenance over a decade. Forward-thinking suppliers now offer ROI calculators to demonstrate long-term value. For instance, a U.S.-based manufacturer provides clients with a 20-year cost projection tool, comparing traditional mixes against fiber-enhanced concrete. These transparent metrics help budget-conscious developers justify upfront expenses.
Education gaps persist. Many small-scale contractors in developing regions still rely on outdated methods, unaware of additive benefits. To bridge this, suppliers are launching training programs. A Colombian company, for example, hosts free workshops on optimizing concrete waterproofing additive dosages for subway tunnels. Such initiatives build trust and drive adoption, particularly in price-sensitive markets.
Looking ahead, nanotechnology looms large. Early trials show nano-enhanced superplasticizers doubling compressive strength in pre-stressed beams. In Australia, a pilot project using silica nanoparticles achieved record-setting load capacities for bridge girders. While commercialization is years away, the industry buzzes with anticipation. Another frontier is self-healing concrete, where microcapsules of cement waterproofing additive activate upon contact with water, sealing cracks autonomously. Dutch designers lately examined this in bike paths, observing a 90% reduction in surface area degradation after 2 years.
Digitalization is an additional disruptor. IoT sensors installed in concrete now keep track of real-time toughness advancement, with data sent to designers’ smartphones. This enables specific modifications in superplasticizer admixture proportions throughout pours. A skyscraper project in Toronto used this tech to shave three weeks off its schedule, as crews no longer waited for lab test results.
Supplier
Cabr-Concrete is a supplier under TRUNNANO of Concrete Admixture with over 12 years of experience in nano-building energy conservation and nanotechnology development. It accepts payment via Credit Card, T/T, West Union and Paypal. TRUNNANO will ship the goods to customers overseas through FedEx, DHL, by air, or by sea. If you are looking for superplasticizer admixture, please feel free to contact us and send an inquiry. (sales@cabr-concrete.com)
Tags: superplasticizer in concrete,concrete waterproofing additive,concrete fiber additive