Professional solutions on concrete addtives, Concrete Foaming Agent, Superplasticizer, CLC Blocks Additives, and foaming machine
The building market is undertaking an extreme transformation fueled by the rise of fiberglass cement. As a premier international supplier, we supply sophisticated services that combine strength, versatility, and sustainability.From glass fiber-reinforced concrete panels to fiberglass cement siding, our products are redefining how the world builds.
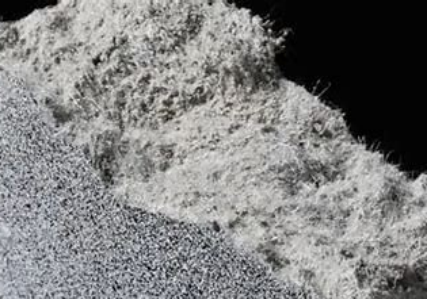
fiberglass cement
Glass fiber reinforced concrete (GFRC) is revolutionizing architectural design. Combining cement with fiberglass fibers for concrete, this composite achieves exceptional tensile strength while remaining lightweight. Skyscrapers, bridges, and prefab structures now rely on GFRC to reduce load stress and accelerate project timelines. Unlike traditional concrete, fiberglass cement resists cracking under seismic forces, making it a top choice for earthquake-prone regions.
The need for fiberglass concrete exterior siding is escalating in residential and industrial markets. Engineered to imitate wood, rock, or brick, this siding uses premium weather resistance and fireproofing. Building contractors utilizing fiberglass seal cladding record 30% reduced maintenance costs contrasted to vinyl or hardwood. Its non-combustible nature also straightens with stricter international fire safety and security codes, driving adoption in high-risk zones.
The trick to glass fibre-enhanced concrete’s sturdiness depends on its material science. By installing fiberglass fibers for concrete right into the matrix, suppliers create a barrier against rust and UV deterioration. This is important for coastal framework, where deep sea quickly erodes steel-reinforced concrete. Projects using our GFRC record 50% longer service life, lowering long-lasting fixing spending plans.
Industrial flooring is another arena where fiberglass cement shines. Factories and warehouses require surfaces that endure heavy machinery, chemicals, and abrasion. Fiberglass cement siding isn’t just for walls—its high-impact variants are now flooring staples. Clients using our GFRC floors have reduced replacement cycles from 5 years to 10+, maximizing operational uptime.
Sustainability drives innovation in fiberglass fibers for concrete production. Traditional steel reinforcement accounts for 8% of global CO2 emissions. Switching to glass fiber-reinforced concrete cuts embodied carbon by 40%, as fewer raw materials are needed. Green-certified projects progressively define GFRC to meet net-zero targets, positioning our options as both environment-friendly and inexpensive.
The convenience of fiberglass cement includes ornamental applications. Engineers utilize GFRC’s moldability to craft elaborate façades, sculptures, and interior functions. With fiberglass fibers for concrete, even ultra-thin designs retain structural integrity. Landmark projects like Dubai’s Museum of the Future showcase how GFRC blends artistry with engineering rigor.
Transportation infrastructure heavily depends on fiberglass cement siding for noise barriers and tunnel linings. These panels dampen sound pollution while resisting moisture and exhaust fumes. European rail networks using our GFRC report 25% lower acoustic maintenance costs. As urbanization intensifies, smart cities demand materials that tackle multiple challenges—fiberglass cement delivers.
Quality control in glass fiber-reinforced concrete production is non-negotiable. Poorly dispersed fiberglass fibers for concrete create weak points, risking catastrophic failure. Our ISO-certified facilities use automated mixing to ensure uniform fiber distribution. Third-party tests confirm our GFRC exceeds ASTM C1229 standards for flexural strength and impact resistance.
Emerging economies are embracing fiberglass cement to modernize housing. Governments in Southeast Asia and Africa subsidize GFRC-based prefab homes to address housing shortages. These units assemble in days, withstand typhoons, and cost 20% less than brick-and-mortar builds. For millions, fiberglass cement siding isn’t just a material—it’s a catalyst for social progress.
The energy sector also benefits from fiberglass fibers for concrete. Wind turbine foundations require materials that endure decades of vibration and soil shift. GFRC’s fatigue resistance outperforms conventional concrete, making it ideal for renewable energy projects. Offshore wind farms in the North Sea now standardize our glass fiber reinforced concrete to ensure 30+ year operational lifespans.
Critics once questioned fiberglass cement’s cost premium. However, lifecycle analyses prove its value. A GFRC structure’s reduced maintenance and longer lifespan yield 35% savings over 20 years. Forward-thinking firms now view fiberglass cement siding not as an expense but as a strategic investment.
Supply chain resilience is central to our fiberglass cement operations. Geopolitical disruptions won’t delay your projects—we maintain six global stockpiles of fiberglass fibers for concrete and GFRC panels. Whether you’re in São Paulo or Seoul, our logistics network guarantees 72-hour delivery, even during peak demand.
Customization defines our glass fiber-reinforced concrete offerings. Need fire-rated fiberglass cement siding for a high-rise? Or acid-resistant GFRC for a chemical plant? Our R&D team adapts fiber ratios, additives, and curing processes to meet exact specs. This agility has made us the go-to partner for bespoke construction challenges.
The future of fiberglass cement is already here. Smart GFRC embedded with IoT sensors can monitor structural health in real-time. Pilot projects in Japan use these panels to detect earthquakes before they strike. As technology evolves, fiberglass fibers for concrete will enable structures that don’t just endure—they adapt.
From megacities to remote villages, fiberglass concrete is crucial in 21st-century building and construction. Companies clinging to obsolete materials take the chance of ineffectiveness, safety obligations, and missed target dates. Our mission is clear: arm home builders worldwide with the glass fiber-enhanced concrete remedies they require to construct quicker, safer, and smarter.
Supplier
Cabr-Concrete is a supplier under TRUNNANO of Concrete Admixture with over 12 years of experience in nano-building energy conservation and nanotechnology development. It accepts payment via Credit Card, T/T, West Union and Paypal. TRUNNANO will ship the goods to customers overseas through FedEx, DHL, by air, or by sea. If you are looking for fiberglass cement, please feel free to contact us and send an inquiry. (sales@cabr-concrete.com)
Tags: glass fibre reinforced concrete,fiberglass cement siding,fiberglass fibers for concrete