Professional solutions on concrete addtives, Concrete Foaming Agent, Superplasticizer, CLC Blocks Additives, and foaming machine
As a lightweight porous building material, foamed concrete is widely used in the field of building energy conservation due to its excellent thermal insulation performance, good seismic performance and low density. As a key material for the preparation of foamed concrete, the performance of the foaming agent directly affects the pore structure and final performance of foamed concrete. With the increasing demand for green building materials and the improvement of environmental protection requirements in the construction industry, the development of high-performance and environmentally friendly concrete foaming agents has become a research hotspot.
At present, the concrete foaming agents on the market are mainly divided into three types: animal protein, plant protein and synthetic. There are significant differences in the source of raw materials, production process, performance characteristics and application effects of various types of foaming agents. This paper aims to systematically analyze the preparation process, action mechanism and performance characteristics of different types of concrete foaming agents and provide a theoretical basis and technical reference for selecting suitable foaming agents in engineering applications through comparative studies.
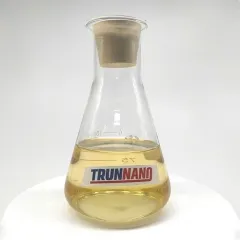
Classification and basic characteristics of concrete foaming agents
Concrete foaming agents can be divided into three categories according to the source of raw materials and chemical composition: protein foaming agents (including animal protein and plant protein), synthetic surfactant foaming agents and composite foaming agents. Protein foaming agents are mainly derived from the hydrolyzate of animal and plant proteins and have good biodegradability and environmental friendliness; synthetic foaming agents are surfactants prepared by chemical synthesis methods and have the characteristics of strong foaming ability and stable performance; composite foaming agents are composed of different types of foaming agents by physical or chemical methods, aiming to combine the advantages of each component.
The action mechanism of foaming agents in concrete mainly includes three aspects: reducing surface tension, forming directional adsorption film and increasing liquid phase viscosity. High-quality foaming agents should have the following characteristics: high foaming multiple, good foam stability, strong compatibility with cement, small effect on concrete strength, environmental protection and non-toxicity. These characteristics of foaming agents directly affect the porosity, pore size distribution, mechanical properties and durability of foamed concrete. Therefore, choosing a suitable foaming agent is crucial to the preparation of high-performance foamed concrete.
Analysis of the characteristics of animal protein foaming agents
Animal protein foaming agents are usually made from animal hoof horns, hair, blood, etc., and are made through processes such as hydrolysis, degreasing and concentration. Its production process mainly includes raw material pretreatment, alkaline hydrolysis, pH adjustment, concentration and drying. The main active ingredients of this type of foaming agent are polypeptide chains and amino acids with moderate molecular weight. They are rich in active groups such as carboxyl and amino groups and can form a strong adsorption film at the gas-liquid interface.
The advantages of animal protein foaming agents are mainly reflected in excellent foam stability, good compatibility with cement paste, and little damage to concrete strength. Because the active groups contained in its molecular structure can interact with cement hydration products, the foam wall strength formed is relatively high. However, this type of foaming agent also has obvious disadvantages: poor temperature resistance and easy decomposition at high temperatures; limited raw material sources; large performance fluctuations between product batches; some products have an odor, etc.
In terms of application effect, foamed concrete prepared using animal protein foaming agents usually has a more uniform pore size distribution, a higher closed porosity and good mechanical properties. Studies have shown that when the foaming multiple is 20-30 times, the 28-day compressive strength of foamed concrete prepared by animal protein foaming agent can reach 3-5MPa, and the thermal conductivity is between 0.08-0.12W/(m·K), showing excellent comprehensive performance.
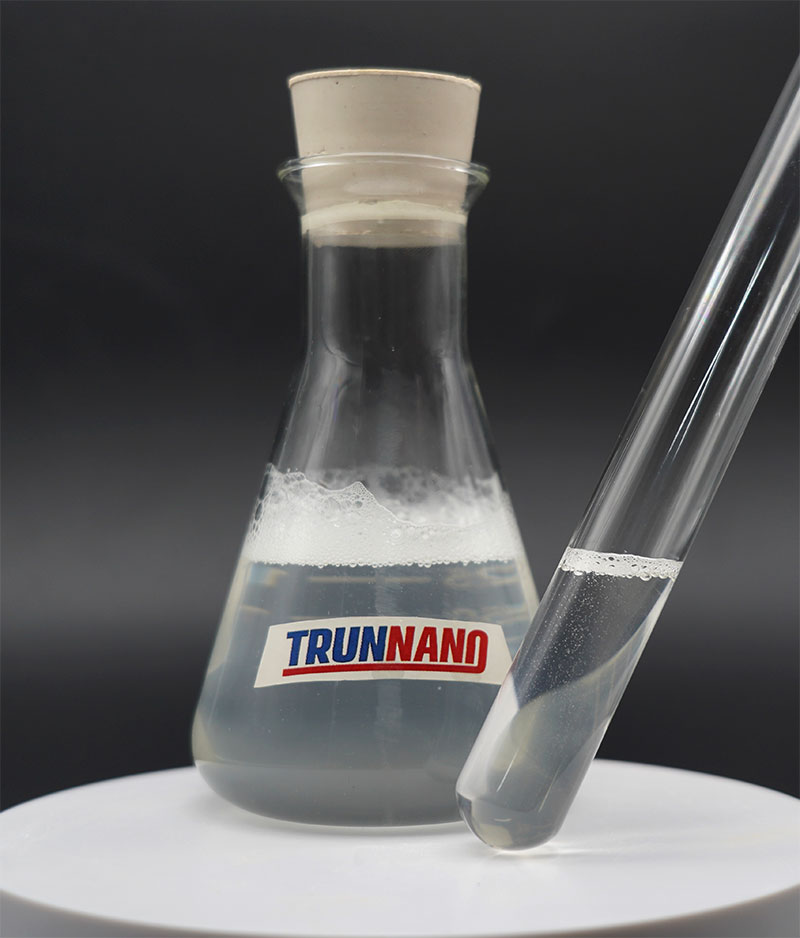
Analysis of the characteristics of plant protein foaming agent
Plant protein foaming agent is mainly made of plant proteins such as soybean protein, cottonseed protein, rapeseed protein, etc., and is prepared by extraction, modification and other processes. Compared with animal protein foaming agents, the production process of plant protein foaming agents is more environmentally friendly, and the source of raw materials is wider and more sustainable. The typical preparation process includes protein extraction, enzymatic or chemical hydrolysis, modification treatment and other steps, among which modification treatment is the key link to improve foaming performance.
The molecular structure of plant protein foaming agents is characterized by containing more hydrophilic amino acid residues and a wide molecular weight distribution. Its surface activity can be improved through appropriate modification treatments, such as acylation and phosphorylation. The advantages of this type of foaming agent are that the raw materials are renewable, environmentally friendly and non-toxic, the price is relatively low, and the product has no odor. But its disadvantages are also obvious: the foaming performance of natural plant protein is usually not as good as animal protein; it is greatly affected by the variety and origin of raw materials; and some products have insufficient foam stability.
In practical applications, the pore size of foamed concrete prepared by plant protein foaming agents is relatively large, but by optimizing the mix ratio and process parameters, products with satisfactory performance can still be obtained. Studies have shown that plant protein foaming agents using special modification processes can control the dry density of foamed concrete within the range of 300-800kg/m³, the compressive strength reaches 1.5-4.0MPa, and the thermal conductivity is 0.10-0.16W/(m·K), which can basically meet the requirements of most building insulation applications.
Characteristic analysis of other types of concrete foaming agents
Synthetic surfactant foaming agents are another important category of concrete foaming agents, mainly including anionic (such as sodium dodecyl sulfate), nonionic (such as fatty alcohol polyoxyethylene ether) and zwitterionic surfactants. This type of foaming agent is prepared by chemical synthesis and has the characteristics of clear molecular structure, high purity and stable performance. Its biggest advantage is strong foaming ability, fast foaming speed, good product consistency, and is not restricted by seasonality and regionality of raw materials. However, synthetic foaming agents are generally poor in biodegradability, some products may pollute the environment, and their compatibility with cement paste is not as good as protein foaming agents.
Composite foaming agents are developed to overcome the shortcomings of single-foaming agents. They are made by compounding different types of foaming agents in a specific proportion or adding additives such as foam stabilizers and enhancers. The design concept of this type of foaming agent is to combine the advantages of each component to achieve complementary performance. For example, compounding animal protein foaming agents with synthetic surfactants can not only maintain good foam stability but also improve foaming efficiency; adding polymer foam stabilizers to plant protein foaming agents can improve their foam stabilization performance. The performance of composite foaming agents is usually better than that of single components, but the cost is relatively high, and the formula design is more complicated.
In addition, there are some special types of foaming agents, such as polymer microsphere foaming agents, chemical foaming agents, etc. Polymer microsphere foaming agents introduce bubbles by adding pre-prepared polymer hollow microspheres into concrete. This method can accurately control the porosity and pore size distribution, but the cost is expensive. Chemical foaming agents form pores by chemical reactions in concrete to produce gases (usually hydrogen or nitrogen). This method is complex and difficult to control and is rarely used in concrete.
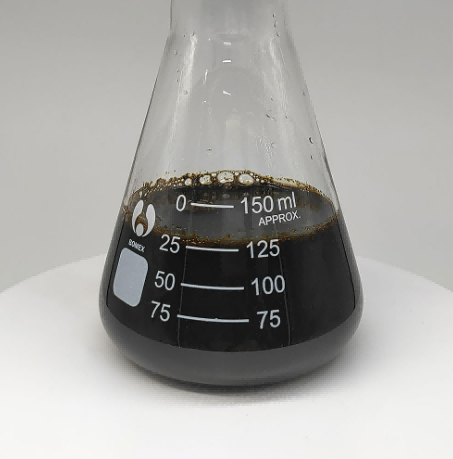
Performance comparison and application selection of various foaming agents
From the perspective of foaming performance, synthetic foaming agents usually have the highest foaming multiple, which can reach 30-50 times; animal protein foaming agents are second, about 20-30 times; plant protein foaming agents are relatively low, generally 15-25 times. However, in terms of foam stability, animal protein foaming agents perform best, with a foam half-life of more than 4 hours; plant protein foaming agents are about 2-3 hours, and synthetic foaming agents are usually less than 1 hour and need to add foam stabilizers to improve.
In terms of the impact on concrete performance, protein foaming agents have less negative impact on concrete strength due to their ability to interact with cement hydration products, especially the foamed concrete prepared by animal protein foaming agents has the highest strength. Although synthetic foaming agents have good initial foaming effects, the lack of such interaction often leads to a significant reduction in concrete strength. In terms of durability, protein foaming agents also show advantages, and foamed concrete prepared by them usually has better freeze-thaw cycle resistance and drying shrinkage performance.
From an environmental perspective, plant protein foaming agents are the most environmentally friendly, with renewable raw materials, low energy consumption in the production process, and completely biodegradable products; animal protein foaming agents are second, although the raw materials come from animal by-products, but overall they are still relatively environmentally friendly; synthetic foaming agents are the worst in environmental protection, and some products may even cause environmental hormone problems. In terms of economy, plant protein foaming agents have the lowest cost, followed by animal protein, and synthetic and composite foaming agents have higher costs.
When selecting a foaming agent in an actual project, the following factors should be considered comprehensively: concrete performance indicators required by the project (such as density, strength, thermal conductivity, etc.), construction conditions (such as temperature, mixing method etc.), cost budget, and environmental protection requirements. Generally speaking, animal protein foaming agents are suitable for structural foam concrete with high strength requirements; plant protein foaming agents can be considered for ordinary thermal insulation purposes; when rapid and large-scale foaming is required, synthetic foaming agents can be selected; when there are special requirements for performance, composite foaming agents can be selected.
Supplier
Cabr-Concrete is a supplier under TRUNNANO of Concrete Admixture with over 12 years of experience in nano-building energy conservation and nanotechnology development. It accepts payment via Credit Card, T/T, West Union and Paypal. TRUNNANO will ship the goods to customers overseas through FedEx, DHL, by air, or by sea. If you are looking for XXX, please feel free to contact us and send an inquiry. (sales@cabr-concrete.com)