Professional solutions on concrete addtives, Concrete Foaming Agent, Superplasticizer, CLC Blocks Additives, and foaming machine
As a lightweight, porous material with good thermal insulation performance, foam concrete has been widely used in construction, roads, bridges and other fields. However, due to its unique structural characteristics, foam concrete is prone to cracking during use, which not only affects its aesthetics but may also have an adverse effect on the stability and durability of the structure. Therefore, taking effective anti-cracking measures is crucial to ensure the performance of foam concrete and extend its service life. The following are some of the main anti-cracking measures for foam concrete:
1. Raw material selection and quality control
First of all, controlling the quality of foam concrete from the source is the key to preventing cracking. Raw materials with stable quality and excellent performance should be selected, including cement, foaming agent, admixture, etc. As a cementitious material, its quality directly affects the strength and durability of concrete. Therefore, cement varieties with appropriate strength grade and stable quality should be selected. The selection of foaming agents is equally important, which determines the pore structure and density of foam concrete, which in turn affects its anti-cracking performance. At the same time, the dosage and use method of admixtures should be strictly controlled to ensure their effective function.
2. Adding reinforcing fibers
Adding an appropriate amount of reinforcing fibers, such as cellulose fibers and sisal fibers, to foam concrete can significantly improve the crack resistance of concrete. These fibers can form a mesh structure inside the concrete, increase the toughness and tensile strength of the concrete, and effectively inhibit the generation and development of microcracks. At the same time, the bridging effect of the fibers can also improve the connection effect of the internal structure of the concrete and reduce the stress concentration caused by drying shrinkage.
3. Using reinforcing agents
Reinforcing agents are another effective means to improve the crack resistance of foam concrete. By adding an appropriate amount of reinforcing agents, such as acrylates and carbon fibers, the strength and durability of concrete can be significantly improved. Reinforcing agents can improve the microstructure of concrete and enhance the bonding between cement and aggregate, thereby improving the crack resistance of concrete.
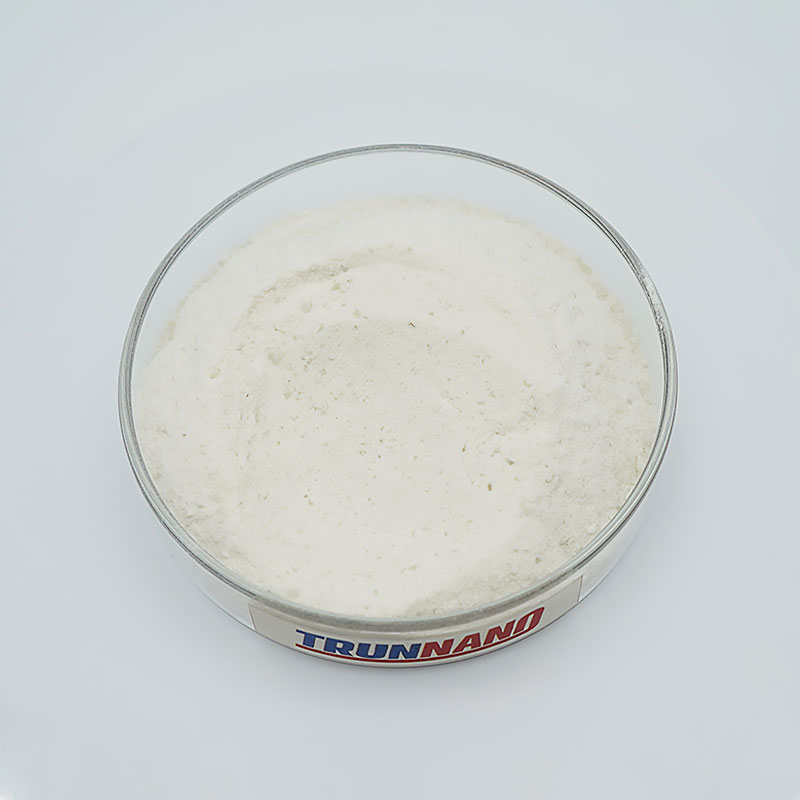
Cement Anti-crack Agent
4. Control the construction environment and process
The construction environment and process of foam concrete also have an important impact on its crack resistance. During the construction process, the ambient temperature and humidity should be strictly controlled to avoid construction under extreme weather conditions. At the same time, the construction plan and pouring process should be reasonably designed to ensure that the concrete is evenly and densely filled into the mold to reduce cracking problems caused by improper construction. In addition, the maintenance of concrete should be strengthened to keep its surface moist and reduce cracks caused by drying shrinkage.
5. Setting a protective layer
Setting a protective layer on the surface of foam concrete is also one of the effective measures to prevent cracking. The protective layer can be achieved by using waterproof and crack-resistant concrete or brushing with penetrating inorganic waterproofing agents. Waterproof and crack-resistant concrete contains high-efficiency waterproofing agents and crack-resistant fibers, which can effectively prevent water penetration and cracks. Penetrating inorganic waterproofing agents can form a dense waterproof layer on the surface of concrete, further improving its crack resistance.
6. Optimizing mix design
Reasonable mix design is the basis for ensuring the performance of foam concrete. By adjusting the amount and proportion of cement, water, foaming agent and admixtures, the performance indicators of concrete, such as pore structure, density and strength, can be optimized, thereby improving its crack resistance. In addition, it is also possible to consider adding an appropriate amount of lightweight aggregates (such as shale ceramsite) and other materials to adjust the internal humidity of the concrete and constrain the deformation of the matrix, further reducing the risk of cracks caused by drying shrinkage.
Supplier of Concrete Admixture
TRUNNANO is a supplier of Cement Anti-crack Agent over 12 years experience in nano-building energy conservation and nanotechnology development. It accepts payment via Credit Card, T/T, West Union and Paypal. TRUNNANO will ship the goods to customers overseas through FedEx, DHL, by air, or by sea. If you are looking for high quality Concrete Admixture, please feel free to contact us and send an inquiry.