Professional solutions on concrete addtives, Concrete Foaming Agent, Superplasticizer, CLC Blocks Additives, and foaming machine
Accelerators are chemical additives mainly used to shorten the setting time of concrete or mortar by accelerating the hydration process of cementitious materials. Common accelerators include calcium chloride, which is one of the most effective accelerators, but it can also be corrosive to steel bars. Non-chloride accelerators such as nitrite and thiocyanate can avoid corrosion problems, but their efficiency may be lower.
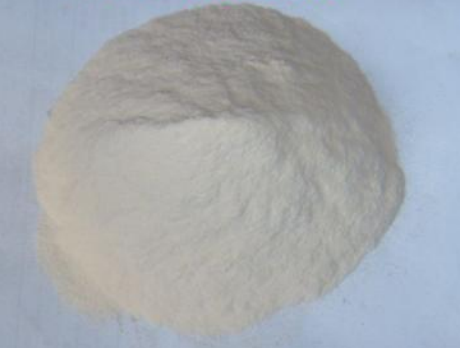
The main advantage of using accelerators is that they can accelerate the construction progress, especially in cold weather conditions where the natural curing process slows down. Accelerators can increase early strength gains, thereby speeding up template removal and advancing traffic loads on the road surface. However, if not properly balanced with other mixed components, they can also lead to long-term strength reduction and increased permeability.
From a chemical point of view, accelerators play a role by shortening the induction period of cement hydration, thus improving the formation rate of hydration products (such as calcium silicate hydrate (C-S-H) gel). The effectiveness of accelerators depends on their compatibility with cement types, water-cement ratio, and the presence of other admixtures in the mixing design.
On the other hand, antifreeze chemicals are specifically designed to protect newly poured concrete from freeze-thaw damage during the initial curing stage. They work by lowering the freezing point of water in the concrete pore system or promoting faster early strength development, which increases resistance to cracking caused by ice expansion.
Parameter | Description/Value |
Product Name | Concrete antifreeze |
Chemical Composition | Calcium nitrate, sodium nitrite, etc. |
Appearance | White powder / Clear liquid |
Density (g/cm³) | 1.20 – 1.35 (for liquid form) |
Solubility in Water | Soluble in water |
Freezing Point Depression (°C) | -10°C to -30°C depending on concentration |
Setting Time | Initial set: [X] hours; Final set: [Y] hours |
Strength Development | 1-day strength: [Z] MPa; 28-day strength: [W] MPa |
Dosage (%) | 2% – 5% of cement weight |
Application Temperature Range (°C) | -5°C to +5°C |
Packaging | 25kg bags / 200L drums |
Storage and Shelf Life | Store in dry place; [X] months shelf life |
Safety Data Sheet (SDS) Information | Available upon request |
Environmental Impact | Low environmental impact; biodegradable |
Concrete Antifreeze Product Specifications
Typical antifreeze agents include air-entraining agents, which introduce microscopic bubbles into the concrete matrix, providing space for water expansion without damaging the structure. Other antifreeze agents may contain antifreeze compounds that can lower the freezing point of water and prevent ice crystal formation even at sub-zero temperatures.
In areas with harsh winter weather, the use of antifreeze is particularly important; otherwise, concrete poured in late autumn or early winter is prone to early failure. In addition, the addition of antifreeze can extend the construction season to colder months, thereby improving project progress and efficiency.
Although both accelerators and antifreeze chemicals play critical roles in concrete technology, they meet different needs and bring their challenges. A key consideration factor is the potential interaction between these additives. For example, some accelerators may interfere with the action of the air-entraining agent, thereby affecting the antifreeze effect. Therefore, ensuring compatibility is crucial when mixing multiple additives.
Another challenge is related to the environmental impact of these chemicals. Traditional accelerators, especially those containing chlorides, pose a corrosion risk to embedded metals and may leach into groundwater. Similarly, certain antifreeze agents may contain harmful substances that may affect soil and water quality. Therefore, people are increasingly emphasizing the development of more environmentally friendly alternatives while minimizing adverse ecological impacts and maintaining performance standards.
The future of accelerators and antifreeze may involve advances in nanotechnology and green chemistry. Nanoparticles can enhance the dispersibility and reactivity of chemical admixtures, thereby improving performance and durability. At the same time, bio-based and recyclable materials provide promising avenues for creating environmentally friendly choices that align with global sustainable development goals.
In addition, the integration of intelligent technologies such as sensors and data analysis can optimize the application of these chemicals by monitoring real-time conditions and adjusting dosages accordingly. These innovations not only improve the efficiency and reliability of construction projects but also contribute to creating a more sustainable building environment.
In short, accelerators and antifreeze chemicals are indispensable tools in modern construction, each with unique advantages and capable of addressing specific challenges. By continuously improving these technologies and exploring new fields in chemistry and materials science, the industry can better adapt to constantly changing environmental conditions and establish a resilient infrastructure that can withstand the test of time. As we move forward, collaboration between researchers, manufacturers, and policymakers is crucial for driving innovation and ensuring responsible use of these powerful building aids.
Supplier
Cabr-Concrete is a supplier under TRUNNANO of Concrete Admixture with over 12 years of experience in nano-building energy conservation and nanotechnology development. It accepts payment via Credit Card, T/T, West Union and Paypal. TRUNNANO will ship the goods to customers overseas through FedEx, DHL, by air, or by sea. If you are looking for Accelerator and Antifreeze, please feel free to contact us and send an inquiry.sales@cabr-concrete.com