Professional solutions on concrete addtives, Concrete Foaming Agent, Superplasticizer, CLC Blocks Additives, and foaming machine
Acrylic acid (CH ₂=CH-COOH) has a conjugated system that endows it with unique properties, making it highly reactive but challenging to handle. Its molecular structure allows for easy polymerization reactions, resulting in the formation of polyacrylic acid and copolymers with other monomers. The presence of double bonds and carboxyl groups provides multiple reaction sites, enabling various synthetic pathways:
Aggregation: Acrylic acid is prone to free radical polymerization to form polyacrylic acid, which has excellent water solubility and strong acidity. Co-polymerization with other monomers can customize the properties of the resulting material for specific applications.
Esterification: Reacts with alcohol to produce acrylic esters, which are widely used in coatings, adhesives, and paints due to their excellent film-forming ability and durability.
Amidation: The formation of acrylamide derivatives has opened up the way for the production of superabsorbent polymers and flocculants, which are crucial for water purification and petroleum extraction operations.
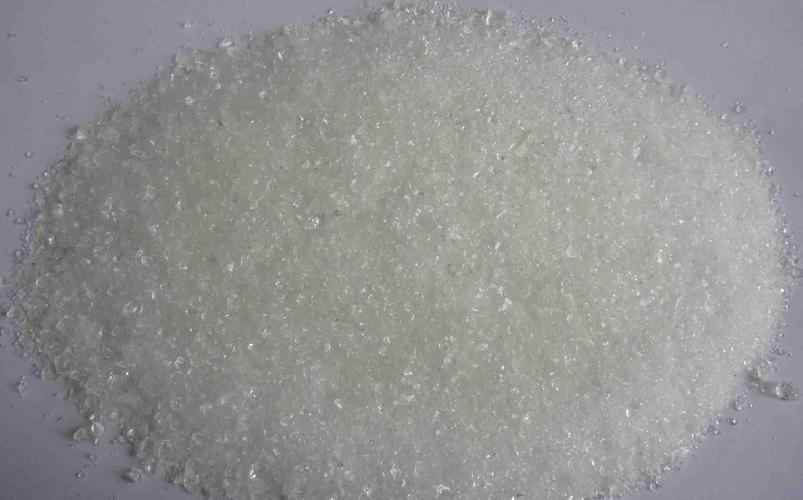
Acrylic acid
Industrial application of acrylic acid
Highly absorbent polymers (SAP): Acrylic based SAP is essential in hygiene products such as diapers and sanitary napkins as they absorb and retain large amounts of water or bodily fluids. These materials can also be used for soil moisture retention in agriculture and leakage control in environmental remediation.
Coatings and adhesives: Acrylic polymers have excellent adhesive strength and weather resistance, making them an ideal choice for the automotive, construction, and electronics industries. Their ability to form flexible films helps to create durable protective coatings.
Textile finishing: Acrylic derivatives can enhance the wrinkle resistance, flame retardancy, and wash resistance of fabrics. They are also used for fixing colors and printing processes.
Water treatment: Polyacrylate-based coagulants help remove suspended solids from wastewater streams, improve transparency, and reduce pollutant levels. In addition, these compounds can inhibit the formation of scale in industrial cooling systems.
Challenges in Acrylic Acid Production: High Utilization and Temperature Control
One of the most important challenges when using acrylic acid is managing the heat generated during extensive use. The polymerization reaction of acrylic acid is highly exothermic, and if not controlled properly, it can release a large amount of heat, leading to an uncontrolled reaction. In industrial environments, this poses serious risks to safety and product quality. The traditional method of controlling temperature in the production process of acrylic acid usually involves external cooling methods such as jacket reactors, heat exchangers, and refrigeration systems. Although effective, these solutions increase the complexity and cost of the manufacturing process. In addition, they may introduce additional fault points that require strict maintenance and monitoring.
Parameter | Specification |
Product Name | Propenoic Acid (Acrylic Acid) |
CAS Number | 79-10-7 |
Chemical Formula | C₃H₄O₂ |
Molecular Weight | 72.06 g/mol |
Appearance | Colorless to slightly yellow liquid |
Odor | Pungent, characteristic odor |
Form | Liquid |
Density (g/cm³, at 25°C) | 1.052 g/cm³ |
Melting Point (°C) | 13-14°C |
Boiling Point (°C) | 141°C |
Flash Point (°C) | 53°C (closed cup) |
pH Value (1% solution) | <2 (strongly acidic) |
Solubility in Water | Completely miscible |
Refractive Index (nD, at 20°C) | 1.428 |
Viscosity (mPa·s, at 25°C) | Approximately 1.0 mPa·s |
Autoignition Temperature (°C) | 427°C |
Vapor Pressure (mmHg, at 25°C) | 4 mmHg |
Application | Monomer for acrylic polymers, superabsorbent polymers, coatings, adhesives, detergents, flocculants |
Packaging | 200L drums, IBC containers, bulk tankers |
Storage Conditions | Store in a cool, dry place away from incompatible materials like oxidizers and strong bases; keep tightly closed |
Shelf Life | Stable when stored properly |
Safety Precautions | Highly corrosive and irritating to skin, eyes, and respiratory system; use appropriate personal protective equipment (PPE); handle in well-ventilated areas; follow safety data sheet (SDS) guidelines |
Product Specifications for Propenoic Acid (Acrylic Acid)
Exploring solutions for temperature-controlled free acrylic acid process
In order to address the limitations of traditional temperature control methods, researchers and engineers have been exploring innovative alternative solutions to achieve high usage rates of acrylic acid without the need for external cooling. Several promising strategies have emerged:
Inherent polymerization control: Developing new catalysts and initiators that inherently regulate reaction rates can alleviate excessive heating. For example, redox initiators that can initiate polymerization at lower temperatures can reduce peak heat release. Similarly, designing a self-limiting polymerization system where the reaction slows down with increasing temperature provides a built-in protective measure against overheating.
Phase transfer catalysis: Using phase transfer catalysts to promote reactions between immiscible phases, facilitating more controllable and efficient polymerization. By reacting in a two-phase medium, heat dissipation occurs naturally through interface exchange, thereby minimizing the need for external cooling.
Microfluidic reactor: The use of microfluidic technology allows for precise control of reaction conditions at the microscale. Microreactors provide enhanced mixing and heat transfer efficiency, allowing for rapid heat dissipation and preventing hotspots. This method supports continuous flow processing, further improving productivity and safety.
Thermally responsive materials: Adding thermally responsive components to the reaction mixture can adjust viscosity and diffusion rate according to temperature changes. As the temperature increases, these materials will change their physical properties to slow down the reaction, effectively acting as internal thermostats.
Process optimization: Advanced computational modeling and simulation tools help optimize reaction parameters and determine the optimal conditions for minimum heat release. Machine learning algorithms can predict and adjust variables in real time, ensuring stable operation even under changing load conditions.
Acrylic acid remains the cornerstone of modern chemistry, driving innovation in different industries. By addressing challenges related to high-temperature processes through intrinsic aggregation control, phase transfer catalysis, microfluidic reactors, thermally responsive materials, and process optimization, transformative solutions have been provided. By exploring these advanced methods, manufacturers can achieve efficient, safe, and sustainable production of acrylic-based materials without the need for complex external temperature control.
Supplier
Cabr-Concrete is a supplier under TRUNNANO of Concrete Admixture with over 12 years of experience in nano-building energy conservation and nanotechnology development. It accepts payment via Credit Card, T/T, West Union and Paypal. TRUNNANO will ship the goods to customers overseas through FedEx, DHL, by air, or by sea. If you are looking for Acrylic acid, please feel free to contact us and send an inquiry.sales@cabr-concrete.com