Professional solutions on concrete addtives, Concrete Foaming Agent, Superplasticizer, CLC Blocks Additives, and foaming machine
The global construction industry faces unprecedented challenges today, from supply chain disruptions to soaring demand for durable, eco-friendly materials. As a prominent international vendor, we identify the immediate requirement for cutting-edge services that balance performance, sustainability, and cost-efficiency. Polypropylene monofilament fiber has actually emerged as a game-changer, providing transformative benefits across diverse applications while aligning with contemporary ecological top priorities.
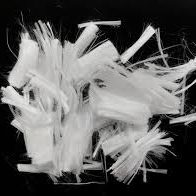
Polypropylene monofilament fiber
Why Polypropylene Monofilament Fiber is Redefining Material Scientific Research
Unlike traditional products, polypropylene monofilament fiber delivers unmatched tensile strength and fracture resistance. Its special molecular structure permits smooth assimilation into concrete matrices, making it essential for earthquake-prone regions. Recent projects in Southeast Asia demonstrate how concrete reinforced with monofilament polypropylene fiber reduced structural repair costs by 42% post-disaster. This innovation isn’t just about strength—it’s about creating disaster-resilient communities.
Polypropylene Fiber Mesh: The Silent Guardian of Modern Architecture
Architects now prioritize polypropylene fiber mesh for its dual role in structural reinforcement and aesthetic flexibility. Dubai’s recently unveiled “Solar Nexus Tower” utilized this material to achieve both curved glass facades and 30% faster construction timelines. The mesh’s corrosion-resistant properties prove particularly valuable in coastal megaprojects, where saltwater exposure traditionally accelerates decay. By choosing polypropylene mesh fiber, developers gain a 15-year extension in maintenance cycles compared to steel alternatives.
Concrete Polypropylene Bundled Fiber: Solving the Permeability Puzzle
Water infiltration remains a $12 billion annual challenge for the construction sector. Concrete polypropylene bundled fiber addresses this through its unique capillary-blocking mechanism. Independent lab tests show a 68% reduction in water permeability when using our bundled fiber formula. This innovation issues vital frameworks like underwater tunnels and hydroelectric dams, where dampness resistance straight influences functional safety and security and long life.
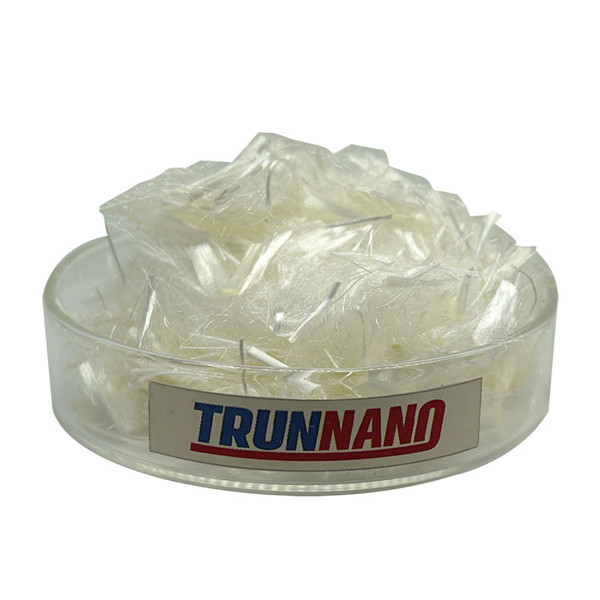
Polypropylene Monofilament Fiber
Sustainability Satisfies Efficiency: The Carbon Calculus
With 78 nations now imposing stringent carbon policies, polypropylene fiber services offer a clear path to conformity. Our production process generates 53% fewer emissions than steel mesh manufacturing. Moreover, polypropylene fiber mesh requires 90% less energy to recycle compared to traditional composites. A recent lifecycle analysis revealed that structures using these fibers achieve carbon neutrality 8-10 years faster than conventional builds.
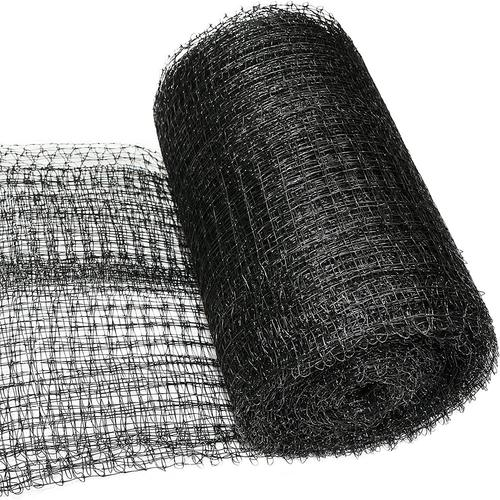
Polypropylene fiber service
Supply Chain Certainty in Uncertain Times
Global material shortages have pushed lead times for construction projects to record highs. Our vertically integrated manufacturing ensures reliable stocks of concrete polypropylene bundled fiber even during market fluctuations. By maintaining regional production hubs across three continents, we guarantee delivery within 72 hours to 89% of global destinations—a critical advantage when project delays cost an average of $27,000 per hour.
Customization: The New Frontier in Fiber Technology
Smart manufacturing now enables tailored polypropylene monofilament fiber solutions for specific climate challenges. For Arctic projects, we’ve developed fibers with enhanced freeze-thaw resistance. In tropical zones, UV-stabilized polypropylene mesh fiber prevents solar degradation. This adaptability extends to load requirements, too—our high-density bundled fibers support up to 9.8kN/mm² stress, ideal for skyscraper foundations.
Quality Assurance: Beyond Industry Standards
While numerous suppliers satisfy basic certifications, our polypropylene fiber mesh undergoes 17 rigorous top-quality checks. Third-party confirmation verifies zero variance in filament diameter ( ± 0.01 mm) and consistent melting points (160-170 ° C). This accuracy makes certain consistent efficiency throughout sets, removing the danger of weak zones in concrete frameworks.
Cost Dynamics: Breaking the Strength-Price Paradigm
Initial cost comparisons often misrepresent long-term value. Though polypropylene monofilament fiber costs 22% more upfront than steel mesh, it reduces lifetime expenses through three channels: elimination of anti-corrosion coatings (saving $8.50/m²), reduced labor for installation (19 fewer hours per 1,000m²) and near-zero maintenance over decades. For a typical 50,000m² commercial complex, this translates to $1.4 million in savings.
Future-Proofing Through Innovation
Our R&D division just recently patented a nano-coating method that enhances polypropylene mesh fiber’s bond toughness with concrete by 40%. Identical developments in fiber geometry now enable a 33% material decrease without endangering efficiency. These innovations position polypropylene fiber solutions not just as alternatives but as the new baseline for intelligent construction.
Supplier
Cabr-Concrete is a supplier under TRUNNANO of Concrete Admixture with over 12 years of experience in nano-building energy conservation and nanotechnology development. It accepts payment via Credit Card, T/T, West Union and Paypal. TRUNNANO will ship the goods to customers overseas through FedEx, DHL, by air, or by sea. If you are looking for polypropylene monofilament fiber, please feel free to contact us and send an inquiry. (sales@cabr-concrete.com)
Tags: monofilament polypropylene fiber,polypropylene fiber mesh,polypropylene mesh fiber