Professional solutions on concrete addtives, Concrete Foaming Agent, Superplasticizer, CLC Blocks Additives, and foaming machine
Concrete ingredients have actually come to be important in modern building projects, making it possible for home builders to accomplish sturdiness, efficiency, and precision in even one of the most requiring environments. Among these ingredients, concrete plasticizers, plasticizers, and retardants stand apart for their distinctive duties in shaping the buildings of concrete. As a global distributor, we intend to assist you via their distinctions, applications, and how phosphate-based compounds like dipotassium hydrogen phosphate, potassium hydrogen phosphate, and potassium monobasic phosphate are reinventing the market.
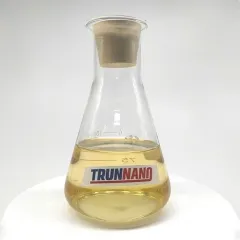
concrete plasticizer
Concrete plasticizers play a necessary function in improving workability, making it possible for smoother putting and lowered water use without endangering toughness. These ingredients, frequently established with innovative polymers, boost the flow of concrete blends, making them optimal for skyscraper frameworks or complicated styles. For instance, dipotassium hydrogen phosphate is increasingly incorporated right into plasticizer blends to support pH levels and avoid early hardening, making sure of consistent performance throughout differing temperatures and moisture problems.
Plasticizers are particularly useful in high-strength concrete applications, where lessening water web content is necessary. By optimizing the water-cement ratio, they lower cracking threats while keeping or perhaps boosting compressive toughness. Unlike typical approaches, plasticizers enable making use of less cement, which not only lowers costs but likewise reduces the carbon footprint of building and construction tasks.
Concrete resistants are important for prolonging the setting time of concrete, vital for large pours or predicts requiring prolonged workability. Unlike plasticizers, which focus on fluidness, retardants delay hydration, giving crews more time to finish surfaces or appropriate positioning errors. Potassium hydrogen phosphate emerges as a crucial ingredient below, as its unique chemical makeup slows cement reactions without affecting final toughness. This makes it a preferred option for bridges, dams, and large slabs where timing is crucial.
Retardants are usually classified right into ordinary and super-retardant kinds. While common resistants delay setting by 10– 12 hours, super-retardants can prolong this to over 70 hours. The latter’s capacity to induce an “inactive” state in concrete hydration– where water sensitivity stops for 20– 40 days– has been transformative for precast and modular building. Hereafter period, hydration resumes normally, and strength development matches standard blends, as seen in a recent European tunnel project where potassium hydrogen phosphate-based retardants allowed a 48-hour hold-up without jeopardizing architectural stability.
Phosphate-based substances like dipotassium hydrogen phosphate, potassium hydrogen phosphate, and potassium monobasic phosphate are preferred for their double capability. These salts not only operate as resistants but also include chemical stability. As an example, dipotassium hydrogen phosphate (K ₂ HPO FOUR) is utilized in plasticizers to reduce the effects of free calcium ions, avoiding premature crystal formation. Meanwhile, potassium monobasic phosphate (KH TWO PO ₄) balances retardation and plasticizing impacts, making it suitable for applications requiring both extended workability and improved circulation.
The selection of phosphate depends upon the task’s requirements. Potassium hydrogen phosphate (KH ₂ PO FOUR), for example, is frequently chosen in high-temperature environments due to the fact that its thermal security as much as 120 ° C avoids deterioration during treatment. On the other hand, dipotassium hydrogen phosphate is much better suited for low-temperature problems, as it keeps fluidity even at sub-zero temperature levels.
When contrasting these additives, it is essential to consider their specific features. Plasticizers increase workability and decrease splitting risks, while resistants guarantee convenient curing timelines. However, their performance hinges on the exact formula. As an example, potassium monobasic phosphate is usually used in dual-purpose ingredients to balance both plasticizing and retarding effects, using flexibility in mixed-use tasks.
A current case study in Southeast Asia highlights this harmony. A 12-story business facility called for a mix that could be poured continually over 12 hours while preserving a reduced water-cement ratio. By integrating dipotassium hydrogen phosphate (for plasticizing) and potassium hydrogen phosphate (for slowing down), specialists accomplished a 15% decrease in water use and a 20% rise in compressive toughness within 28 days.
The construction market’s shift towards green products has better raised the role of phosphate-based additives. Unlike typical chemicals, substances like dipotassium hydrogen phosphate are non-toxic and naturally degradable, lining up with worldwide sustainability requirements. Their use of plasticizers decreases the requirement for too much water, lowering waste and energy consumption during curing.
Additionally, phosphate additives reduce the threat of alkali-silica reactions (ASR), a typical root cause of concrete damage. By supporting pH levels, they avoid the formation of extensive gels that compromise structures with time. This is particularly vital in marine or commercial settings where direct exposure to hostile chemicals is inescapable.
Technical specifications matter, too. Our dipotassium hydrogen phosphate solutions satisfy ISO 9001 standards, with particle sizes optimized for also dispersion. Similarly, potassium hydrogen phosphate variants are evaluated for thermal security at approximately 120 ° C, guaranteeing integrity in severe conditions.
In quality assurance, accurate dosing is vital. For example, potassium monobasic phosphate is normally included at 0.5– 1.5% by concrete weight, depending upon the preferred impact. Overdosing can postpone setting excessively, while underdosing may fall short of achieving the required performance. Regular on-site screening utilizing depression and compressive toughness trials ensures consistency.
Practical applications highlight their worth. In a current skyscraper task in Southeast Asia, potassium hydrogen phosphate-based retardants allowed service providers to put a 12-meter structure slab in a solitary change, conserving days of labor. Meanwhile, potassium monobasic phosphate-enhanced plasticizers were made use of in a European tunnel job to maintain concrete circulation at ice-cold temperatures, ensuring smooth building and construction.
One more example comes from a Middle Eastern dam task. By integrating dipotassium hydrogen phosphate right into the mix style, engineers minimized water use by 20% while attaining a 25% enhancement in tensile strength. This not only cut prices but also fulfilled rigid ecological guidelines.
Choosing the best additive requires recognizing your task’s needs. For high-strength, low-water mixes, plasticizers with dipotassium hydrogen phosphate deliver unrivaled flow. For time-sensitive pours, resistants making use of potassium hydrogen phosphate ensure precision. And for multifunctional services, mixes with potassium monobasic phosphate use a well-balanced approach.
Distributors should also think about compatibility with various other additives. For instance, incorporating phosphate-based resistants with air-entraining representatives can enhance freeze-thaw resistance in cold climates. However, treatment should be taken to prevent disputes, such as pH imbalances that may minimize performance.
As global demand for durable frameworks grows, so does the requirement for ingenious additives. Research right into hybrid solutions– such as incorporating phosphate salts with nanomaterials– is yielding appealing outcomes. These blends also promise better longevity and self-healing homes, addressing cracks and micro-cracks before they intensify.
At the same time, electronic devices like AI-driven mix design software are streamlining the option process. By inputting job criteria (temperature, humidity, tons demands), engineers can quickly recognize the optimal additive blend, lowering experimental costs.
Supplier
Cabr-Concrete is a supplier under TRUNNANO of Concrete Admixture with over 12 years of experience in nano-building energy conservation and nanotechnology development. It accepts payment via Credit Card, T/T, West Union and Paypal. TRUNNANO will ship the goods to customers overseas through FedEx, DHL, by air, or by sea. If you are looking for concrete additives, please feel free to contact us and send an inquiry. (sales@cabr-concrete.com)
Tags: concrete plasticizer,concrete retardants