Professional solutions on concrete addtives, Concrete Foaming Agent, Superplasticizer, CLC Blocks Additives, and foaming machine
PRODUCT PARAMETERS
Description
Introduction of Aramid Fiber
Aramid fiber (also known as aromatic nylon) is a new type of high-tech synthetic fiber with excellent properties such as ultra-high strength, high modulus, high-temperature resistance, acid and alkali resistance, lightweight, insulation, anti-aging, and long life cycle.
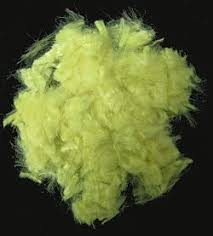
Function of Aramid Fiber
1. Aramid fiber has excellent properties such as soft texture, low density, high strength, high modulus, acid and alkali resistance, and lightweight.
2. In terms of high-temperature resistance, it can be used for more than 10 years at 220 degrees, and it will not decompose or melt at a temperature of 560 degrees.
3. The strength of aramid fiber is 5 to 6 times that of steel wire,
4. The modulus of aramid fiber is 2 to 3 times that of steel wire or glass fiber,
5. The toughness of aramid fiber is 2 times that of steel wire,
6. The weight of aramid fiber is only about 1/5 of that of steel wire.
7. Aramid fiber has good insulation and anti-aging properties and has a long life cycle.
Parameters of Aramid Fiber
Full name | Polyphenylene phthalate | Properties | Insulation, anti-aging performance |
Properties | Aramid chain accounts for more than 85% of the fiber | Elastic modulus | 125-135GPa |
Density | 1.44-1.45Mg/m3 | Yield strength | 2250~2750GPa |
Elongation at break | 2.7%~2.9% | Specific heat | 1350~1450J/kgK |
Temperature resistance | 200-300℃ | Coefficient of thermal expansion | (-4)~(-2)10-6/K |
Thermal conductivity | 0.2~0.3w/mk |
Application of Aramid Fiber
1. Projects with high crack resistance requirements, such as concrete pavement, bridge decks, airport runways, and factory floors.
2. Engineering projects that use special construction methods for walls, roofs, reservoirs, etc. of tunnels and mines.
3. Water conservancy projects such as rivers, dams, dock revetments, bridge piers, etc.
4. Military protection projects, etc.
Usage of Aramid Fiber
Concrete mixing process: add aggregate → add fiber → add cement → add water → stir → add water. Disperse all the fibers.
Mixing time: When making fiber mortar/concrete, the mixing time should be appropriately increased by 30-60 seconds, and commercial concrete does not need to be extended.
Construction Technical Requirements
1. The cement grade shall not be less than 425. The water-cement ratio shall not be greater than 0.5.
2. The diameter length of the coarse aggregate shall not exceed 2/3 of the length of the steel fiber.
3. The volume of steel fiber in steel fiber concrete should not be less than 0.5%, generally between 0.5-3%, and 1.5%–2.5% is recommended; that is, the dosage range of each cubic meter of concrete is: 5-30kg, and 15-25kg is recommended.
4. Sea sand shall not be used to mix steel fiber concrete, and chloride salt is strictly prohibited.
5. In addition to the above provisions, other materials used in steel fiber concrete shall comply with the provisions on raw materials used in reinforced concrete in the current specifications.
6. The consistency of steel fiber concrete can be determined by referring to the consistency required for ordinary concrete in similar projects. Its slump value can be smaller than the corresponding ordinary concrete requirement.
7. When the steel fiber concrete cushion layer and surface layer with a flat-head joint structure does not have a foundation reinforcement layer such as ash soil under the cushion layer and meets the following conditions at the same time:
a. The thickness of the cushion layer and surface layer before reduction is not more than 130mm.
b. The thickness of the foundation reinforcement layer is greater than the thickness of the cushion layer. Its thickness can be multiplied by the reduction factor of 0.75, but shall not be less than 50mm
Material requirements: steel fiber and coarse aggregate – stir for 30 seconds – add sand and cement – stir for 30 seconds → add water → stir for 3 minutes
Compacting:
1. When pouring steel fiber concrete, mix and use it, pour continuously, and do not throw the construction joints until the partition joints are reached. It should be vibrated and compacted during pouring
2. Surface finishing, embossed steel fiber concrete has the characteristics of fine coarse aggregate, large sand rate, and random fiber distribution. It is smoothed mechanically to prevent fiber exposure. The embossing process of the embossing machine can also avoid the phenomenon of fiber exposure caused by pulling. After 24 hours, it should be maintained in time according to routine. It should be covered with straw bags in summer and keep warm in winter.
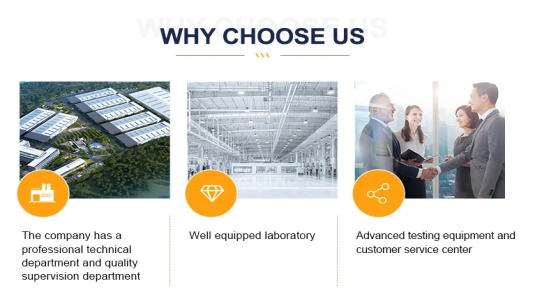
Company Profile
Cabr-Concrete is the global leader in Low-Density Cellular Concrete (LDCC), Celluar Light Concrete (CLC), and advanced engineered foam solutions. Known globally for its commitment to research, innovation, and applied expertise, we have been providing engineered foam solutions since the early 2012’s.
We can supply Concrete Fiber over the world. The company has a professional technical department and quality supervision department, a well-equipped laboratory, and equipped with advanced testing equipment and after-sales customer service center.Send us an email or click on the needed products to send an inquiry.
If you want to know more about Aramid Fiber, please feel free and contact us: sales@cabr-concrete.com
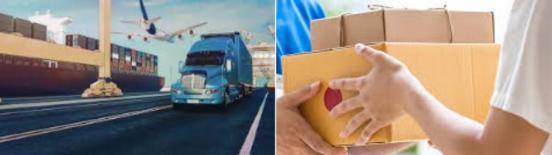
Packaging and Storage of Aramid Fiber
Packaging: Inner plastic bag 0.6kg-2kg per small bag, outer woven bag or carton 10kg-25kg per large bag, 500kg per pallet, can also be produced and packaged according to user requirements.
Payment
T/T, Western Union, Paypal, Credit Card etc.
Shipment
By air, by sea, by express, as customers request.
FAQs of Aramid Fiber
Is aramid fiber flammable?
While aramid fibers have good heat resistance and do not melt, they can burn when exposed to direct flame. However, they tend to char and form an insulating layer that helps prevent the spread of fire.
How is aramid fiber made?
The production process involves spinning a solution of aromatic polyamide into fibers, followed by stretching and heating to align the polymer chains and increase strength.
Can aramid fiber be recycled?
Recycling aramid fiber is challenging due to its complex molecular structure and the high temperatures required to break down the material. However, there are ongoing research efforts to improve recycling methods.
What are the alternatives to aramid fiber?
Other high-performance fibers such as ultra-high molecular weight polyethylene (UHMWPE), carbon fiber, and glass fiber can be used as alternatives depending on the specific requirements of the application.
Who invented aramid fiber?
Aramid fibers were first developed by DuPont in the 1960s. The most well-known brand of aramid fiber is Kevlar, also produced by DuPont
REQUEST A QUOTE
RELATED PRODUCTS
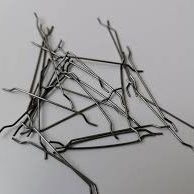
End Hook Steel Fiber for Concrete Reinforcement Steel Fiber
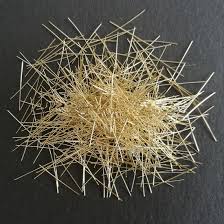
Copper-plated steel fibres
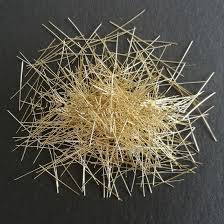
Copper-Coated Microfilament Steel Fiber Fibre for Concrete Use
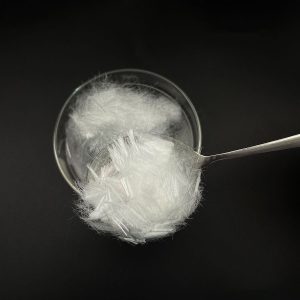
PVA Fibers for Concrete Reinforcement in a Variety of Concrete Mixes
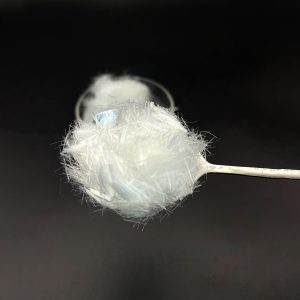
PP Series Polypropylene Crude Synthetic Fiber
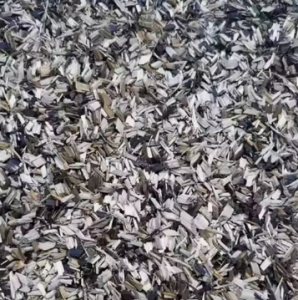