Professional solutions on concrete addtives, Concrete Foaming Agent, Superplasticizer, CLC Blocks Additives, and foaming machine
PRODUCT PARAMETERS
Description
Introduction of Cellulose Fiber
Cellulose fiber is a fiber made from a special plant in high-cold areas through a series of unique chemical treatments and mechanical processing. It is a new type of concrete-specific fiber after chemical synthetic fiber, and is called the third generation of concrete-specific fiber in the engineering industry. Cellulose fiber itself has the characteristics of natural hydrophilicity and high strength and high modulus. Because it is a plant cell that grows naturally through division and growth and is not artificially made, the surface has a strong grip and crack resistance, which can effectively improve the mechanical properties, freeze-thaw resistance and impermeability of concrete.
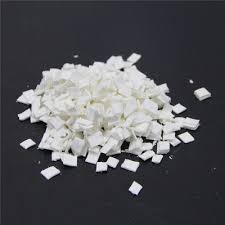
Function of Cellulose Fiber
1. Prevent concrete cracks: Cellulose fiber is distributed in three dimensions in concrete, which can effectively reduce the stress concentration at the tip of microcracks, weaken or eliminate the tensile stress caused by shrinkage of concrete or mortar, and prevent the occurrence and expansion of microcracks.
2. Improvement of concrete impermeability: The uniform distribution of cellulose fiber in concrete forms a support system, which hinders surface water precipitation and aggregate settlement, reduces the water seepage of concrete, reduces the water seepage channel of concrete, and greatly reduces the porosity in concrete, so that the concrete impermeability is significantly improved.
3. Improvement of concrete’s freeze-thaw resistance: The presence of cellulose fiber can effectively reduce the tensile stress concentration in concrete caused by multiple freeze-thaw cycles, preventing further expansion of microcracks. The improvement of concrete’s impermeability is conducive to improving its freeze-thaw resistance.
4. Improve concrete’s impact resistance, flexural resistance, fatigue resistance, and seismic resistance: Cellulose fiber helps absorb the impact of concrete components. Due to the fiber’s crack-blocking effect, when concrete is subjected to impact loads, the fiber can prevent the rapid expansion of internal cracks, so it can effectively enhance the concrete’s impact resistance and toughness.
5. Improve concrete’s durability and aging resistance: Cellulose fiber has a good crack-blocking effect, which greatly reduces the occurrence and development of cracks. The reduction of internal porosity slows down the corrosion and penetration of moisture and chemical media, chloride salts, etc. in the external environment. Due to the large reduction of cracks, the channels for corrosion of the main reinforcement of the structure are reduced, thereby greatly improving and enhancing the durability of concrete.
6. Improve the high temperature resistance of concrete: Add cellulose fiber to high-strength concrete. Because it contains a large number of evenly distributed fiber monofilaments, it presents a three-dimensional random distribution and forms a three-dimensional network structure. When the temperature of concrete rises, the fiber can disperse the expansion force caused by high temperature, which can effectively avoid bursting in a fire environment.
Parameters of Cellulose Fiber
Specific gravity (g/cm) | 1.0-1.2 | Equivalent diameter(um) | 15-25 |
Length (mm) | ≥2 | Breaking strength (MPa) | ≥600 |
Initial modulus (GPa) | ≥7 | Breaking elongation % | 5-20 |
Hydrophilicity | Good | Specific surface area (cm/g) | 20000-30000 |
Safety | Non-toxic and odorless | Acid and alkali resistance | ≥95% |
Application of Cellulose Fiber
1. Water conservancy projects: dams, aqueducts, canals, water services, etc.
2. High-speed railways: bridges, tunnels, ballastless tracks, etc.
3. Industrial and civil buildings: underground structure projects, etc.
4. Marine engineering: cross-sea bridges, port terminals, etc.
5. Others: highways, energy projects, etc.
Usage Method of Cellulose Fiber
Recommended dosage: Design the ordinary concrete mix ratio according to national or industry standards, and prepare fiber concrete according to the designed dosage.
Mixing process: Add aggregate → Add fiber – add water – add cement – stir – add water to make all the fibers dispersed.
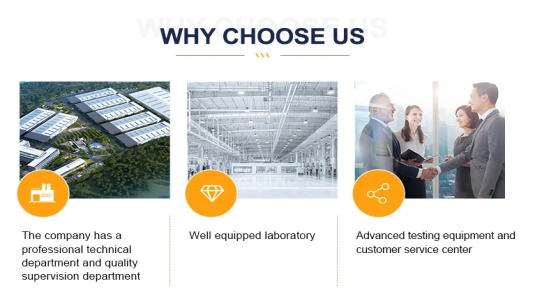
Company Profile
Cabr-Concrete is the global leader in Low-Density Cellular Concrete (LDCC), Celluar Light Concrete (CLC), and advanced engineered foam solutions. Known globally for its commitment to research, innovation, and applied expertise, we have been providing engineered foam solutions since the early 2012’s.
We can supply Concrete Fiber over the world. The company has a professional technical department and quality supervision department, a well-equipped laboratory, and equipped with advanced testing equipment and after-sales customer service center. Feel free and contact us: sales@cabr-concrete.com
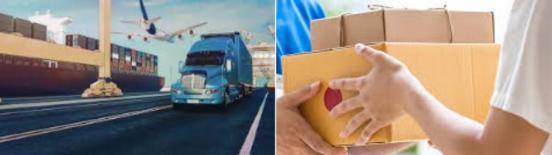
Packaging and Storage of Cellulose Fiber
Packaging: Inner plastic bag 1kg-5kg per small package, outer woven bag or carton 10kg-25kg per package, 500kg per pallet, can also be produced and packaged according to user requirements.
Payment
T/T, Western Union, Paypal, Credit Card etc.
Shipment
By air, by sea, by express, as customers request.
FAQs of Cellulose Fiber
Q: How are cellulose fibers produced?
A: The production process varies depending on the type of cellulose fiber. For example, viscose/rayon involves chemical processing of wood pulp, while lyocell uses a closed-loop system with fewer chemicals. Natural cellulose fibers like cotton and hemp are harvested directly from plants.
Q: Are cellulose fibers eco-friendly?
A: Generally, cellulose fibers are considered more eco-friendly than synthetic fibers due to their biodegradability and renewable source. However, the environmental impact can vary based on how they are produced and the chemicals used in the manufacturing process.
Q: Can cellulose fibers be recycled?
A: Cellulose fibers can be recycled, but the process can be challenging and may involve breaking down the fibers and reforming them, which can affect the quality of the final product.
Q: How do cellulose fibers compare to synthetic fibers?
A: Cellulose fibers offer natural comfort and breathability, making them popular in clothing. They are generally less elastic and may require more care than synthetic fibers, which are known for their durability and stretch.
REQUEST A QUOTE
RELATED PRODUCTS
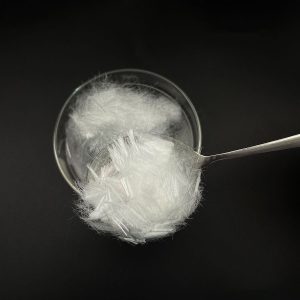
UHPC Special High Performance Polypropylene Synthetic Fiber
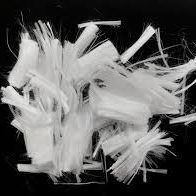
Polypropylene Monofilament Fiber for Concrete
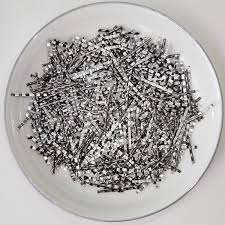
Milling Steel Fiber Mill-Cut Hooked Concrete Steel Fiber Concrete Binder Architecturally Acicular Steel Fiber
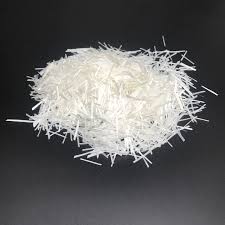
High Quality Fiberglass Chopped Strands Alkali Free Glass Fiber Chopped Strand For Concrete Use
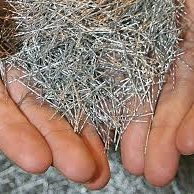
Plastic Steel Fiber Polypropylene Crude Fiber Polypropylene Concrete Reinforcing Fibers Better Than Steel Fiber
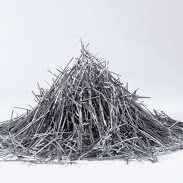