Professional solutions on concrete addtives, Concrete Foaming Agent, Superplasticizer, CLC Blocks Additives, and foaming machine
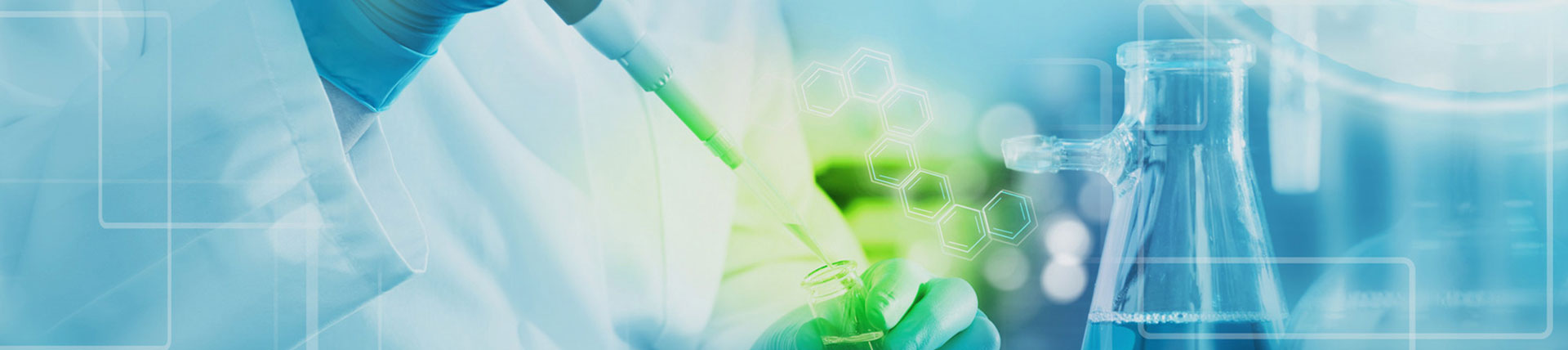
Concrete Release Agent
Overview of Concrete Release Agent
Concrete release agents are specialized coatings applied to formwork and molds used in concrete pouring to facilitate the smooth removal of the cured concrete without causing damage or leaving residue on the forms. They are essential for maintaining the integrity of both the concrete structure and the forms, ensuring a clean and efficient construction process.
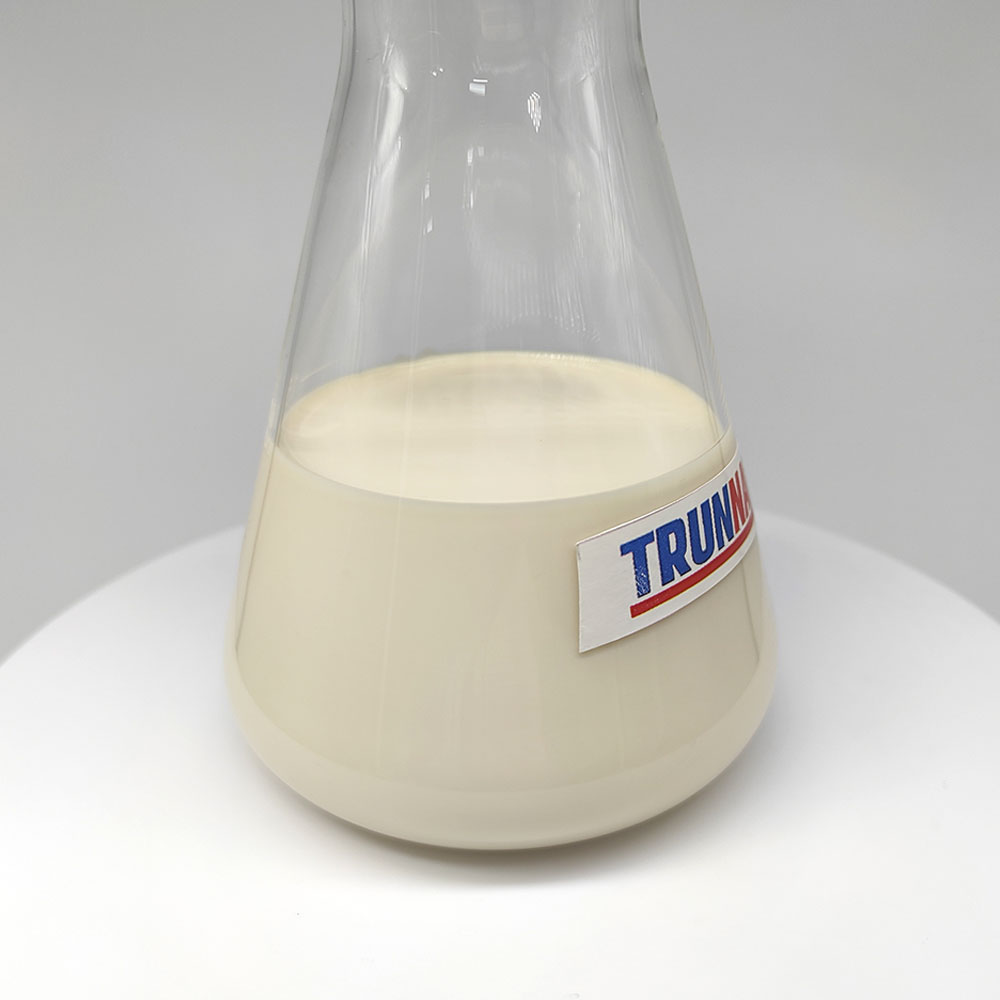
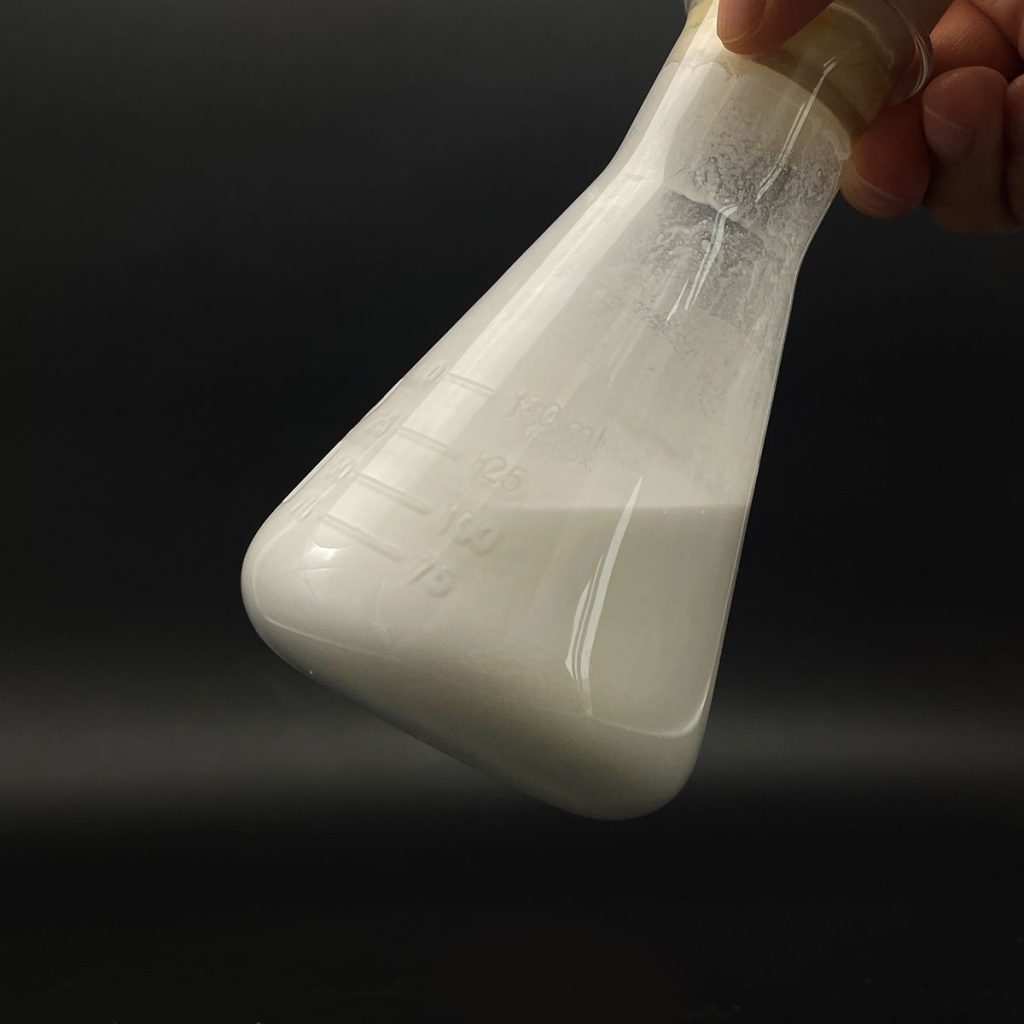
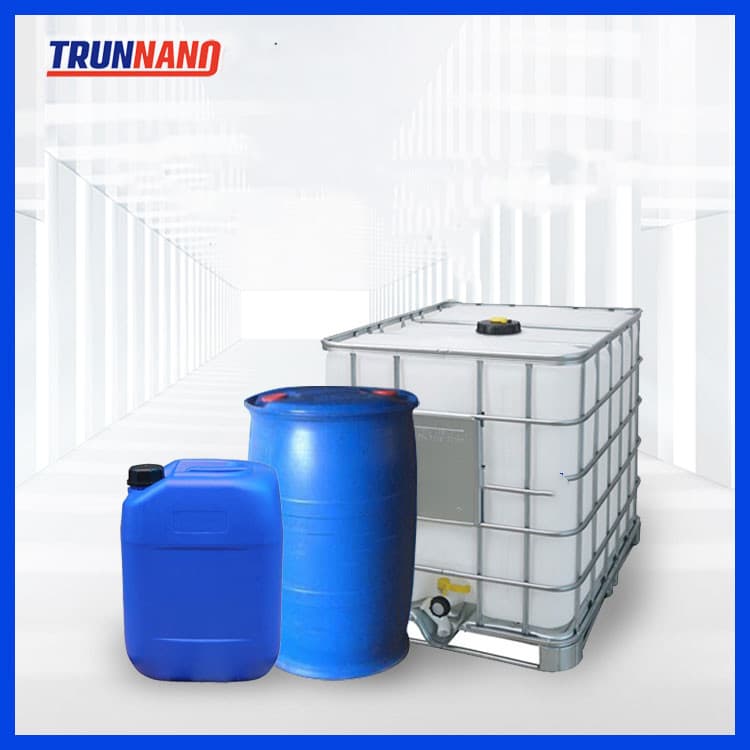
Features of Concrete Release Agent
Environmentally friendly: no volatile organic compounds (VOCs), reducing hazards to the environment and the health of construction workers.
Easy to clean up: easily rinsed off with water after use, leaving no hard-to-remove grease stains or residue.
Cost-effective: water-based products are often more economical and require less water than oil-based release agents.
Versatile: Suitable for use on many types of formwork materials, including wood, metal, plastic and fibreglass reinforced plastic (FRP).
Safety and reliability: non-flammable, reducing the risk of fire; low skin irritation, improving construction safety.
Applications of Concrete Release Agent
- Construction Industry: Commonly used in the casting of concrete structures like walls, pillars, and floors.
- Architectural Precast: Ideal for creating decorative precast elements, where a clean and detailed finish is crucial.
- Bridge and Highway Construction: Essential in forming components for bridges and highways to ensure smooth surfaces and easy form removal.
- Specialty Projects: Used in intricate or artistic concrete projects where the appearance and texture of the finished product are paramount.
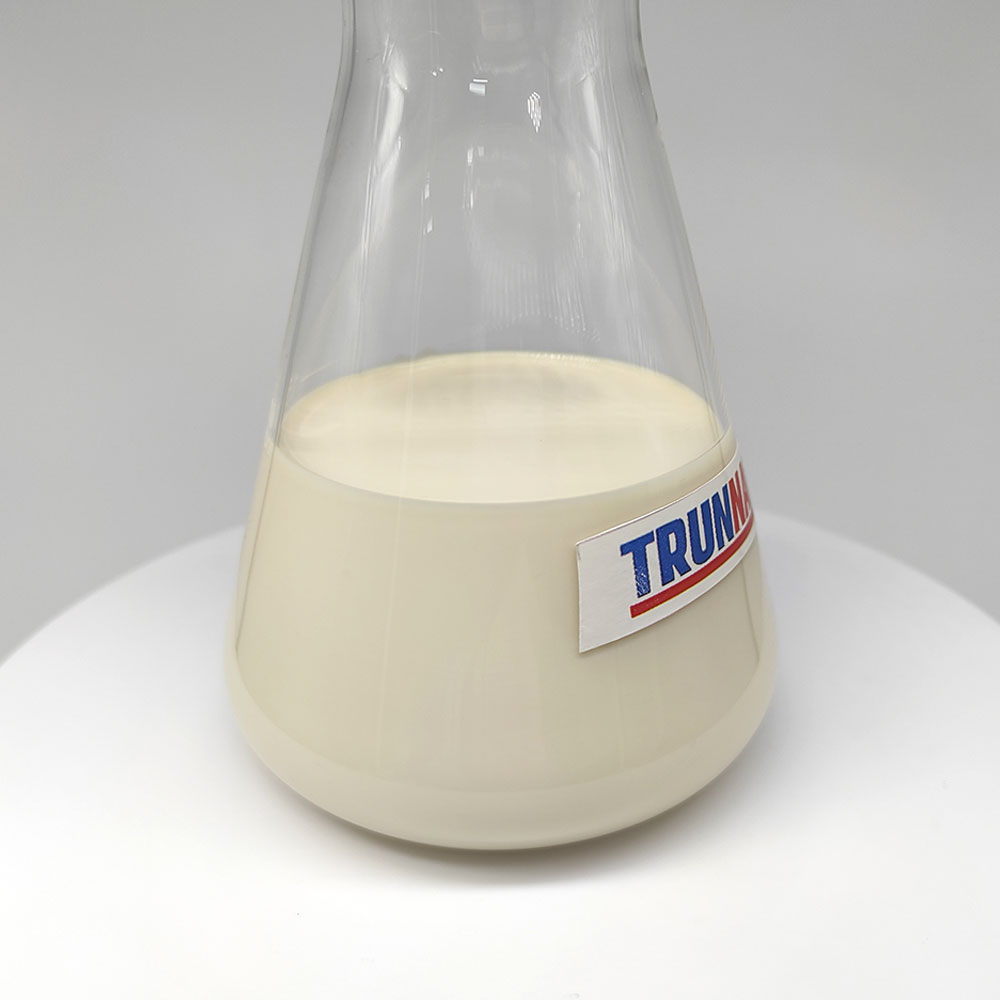
Company Profile
Cabr-Concrete is the global leader in Low-Density Cellular Concrete (LDCC), Celluar Light Concrete (CLC), and advanced engineered foam solutions. Known globally for its commitment to research, innovation, and applied expertise, we have been providing engineered foam solutions since the early 2012's.
We can supply high-quality concrete release agent. The company has a professional technical department and quality supervision department, a well-equipped laboratory, and equipped with advanced testing equipment and after-sales customer service center.Send us an email or click on the needed products to send an inquiry.
If you want to know more about Concrete Release Agent, please feel free and contact us: sales@cabr-concrete.com
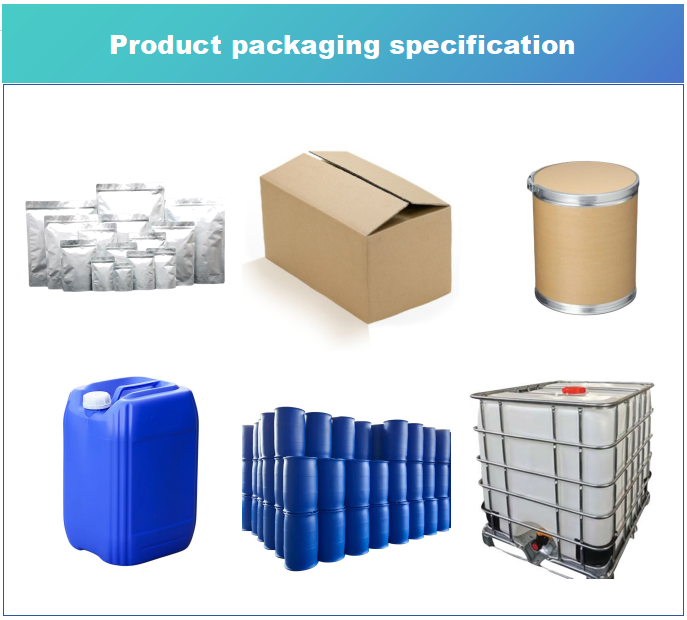
Package of Concrete Release Agent
20Kg/barrel, 200kg/barrel, stored at room temperature away from light, moisture and rain.
FAQs of Concrete Release Agent
What is a good release agent for concrete?
A good concrete release agent should form a lubricating film to prevent concrete from sticking to the formwork without compromising the quality or strength of the concrete. Common release agents on the market include chemically synthesized liquids, emulsions or powders, as well as natural products such as waxes and greases. Consider environmental protection, ease of use and impact on subsequent processes when choosing. A high-quality release agent is not only easy to apply, but also ensures a smooth surface effect and simplifies the demolding process.
Can I use vegetable oil for demolding?
Vegetable oil can be used as a temporary release agent, especially for small DIY projects. Vegetable oil can form a protective layer on the surface of the formwork, reducing the possibility of concrete sticking. However, vegetable oil may affect the curing time and final quality of concrete, resulting in oily residue or color changes on the surface. In addition, it is not the first choice for professional construction because its durability and reliability are not as good as dedicated release agents. It is recommended to decide whether it is suitable for large-scale projects after testing a small area.
How to prevent concrete from sticking to the formwork?
To avoid concrete sticking to the formwork, the formwork surface should be cleaned and dried before pouring to remove rust, dust and other impurities. Then apply an even layer of high-quality release agent. Make sure the release agent completely covers all contact surfaces, but do not apply too much to avoid spillage and contamination of the concrete. For complex shapes or forms that are exposed to the air for a long time, apply multiple thin coats. The correct selection and application of the release agent is key.
What can I use as a binder for concrete?
Common binders for concrete include cement paste, polymer-modified cement-based binders, etc. These materials can enhance the bond between new and old concrete and are particularly suitable for repair work or layered pouring. Polymer-modified binders are popular for their excellent bonding properties and durability. When using, mix according to the manufacturer's instructions, usually adding water and stirring to the appropriate consistency. Concrete laying should be carried out immediately after applying the binder to ensure the best results.